Architect’s Guide to Glass Sustainability
A closer look at embodied carbon, performance considerations, retrofits and recyclability
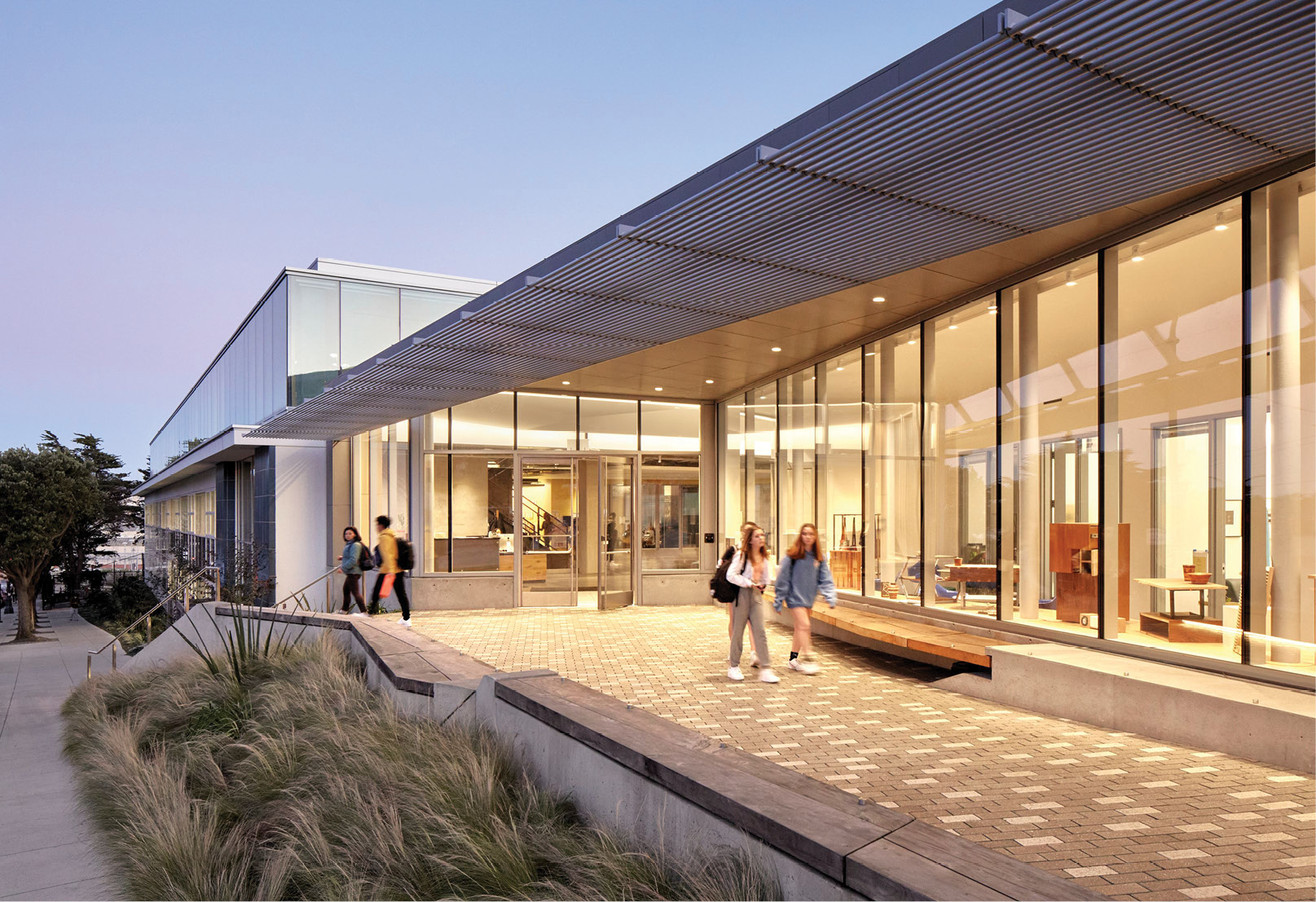
Above: Lick-Wilmerding High School in San Francisco, California, specified Solarban 70 glass to introduce more transparency and daylight. In 2022, the school earned an AIA COTE Top Ten Award for sustainable design excellence. Photo by Michael David Rose Photography.
Globally, the construction industry is responsible for 33% of energy consumption and about 40% of greenhouse gas emissions. So when it comes to addressing climate change by reducing energy consumption and carbon emissions, the building community “has an important job to do,” says Tom Culp, energy code consultant for the National Glass Association and owner of Birch Point Consulting.
The glass and glazing industry plays an essential role in the building community’s efforts to improve efficiency and reduce emissions, says Culp, who was speaking during the panel, “Blueprint for Collaboration: The path towards sustainable facades,” hosted by the NGA the week of the AIA A’23 conference in San Francisco. Culp and the other panelists identified three key areas of focus:
1 | Reduce embodied carbon.
Embodied carbon in construction refers to greenhouse gas emissions caused during the lifecycle of a building product, including raw material extraction, transportation, manufacturing and installation. For the glass industry, the energy-intensive glass manufacturing process is the primary source of embodied carbon.
“Where does embodied carbon come from in glass manufacturing? It’s heat,” says panelist Chris Fronsoe, national architectural team manager, Vitro Architectural Glass. “It’s where raw material goes up to about 3,000 degrees Fahrenheit and gets melted down into liquid material, and later in the float process goes back to solid.” For the manufacture of an insulating glass unit, roughly 75% of embodied carbon is generated during the manufacture of the raw glass lites in the float process due to the energy-intensive nature of the traditional float manufacturing process, says Fronsoe.
Several glass manufacturers have begun to change their processes to lower emissions in manufacturing. Increasing the use of cullet (crushed glass recycled back into the supply chain) in the process reduces the heat required to melt the materials in the furnaces, says Fronsoe. Additionally, a few glass manufacturers, such as Vitro, are using oxy-fuel technology in production, which can reduce energy consumption in glass-melting furnaces by as much as 20% and cut greenhouse gas emissions in half, he says.
2 | Improve operational carbon.
Operational carbon, on the other hand, refers to the emissions produced during a building’s lifespan. The glass industry has made “tremendous progress” in meeting increasingly stringent energy-efficiency requirements in the building codes, says Culp. “In the 20-plus years I’ve been working in energy codes, [the industry] has cut energy use of buildings built to [the ASHRAE 90.1 Standard] by half.”
In terms of thermal performance, the industry offers dual, triple and even quad IGUs. Fabricators have begun using two low-emissivity coatings in the IGUs for increased performance. And the industry continues to invest in next-generation thermal performance solutions, such as vacuum insulating glass and thin-triple IGUs, which provide even better efficiency within a narrow profile.
The glass industry also offers solutions to manage solar heat gain, which impacts building operational carbon. Tinted glass and switchable glass products, such as electrochromics, can further improve operational carbon.
Finally, using renewables will be essential in helping buildings become carbon neutral, or net-zero. Rooftop solar or building-integrated photovoltaics, or BIPV, will help push operational carbon emissions even further. “Efficiency is one half of it, renewables are another,” says Culp.
3 | Increase recycling and reuse.
During the panel, Lisa Rammig, director, Eckersley O’Callaghan, offered insights on how the industry could “reshape the future of glass” through an increase in flat glass recycling and an emphasis on rebuilding facades on existing structures.
Only 6% of flat glass is recycled, according to 2017 estimates from Deloitte. If it is recycled, it is typically downcycled to glass bottles, insulation or road filler. “Glass is a material that is fully and eternally recyclable, so why do we recycle so little flat glass? We need to change the status quo [of glass recycling],” says Rammig.
Additionally, Rammig encourages refurbishment—bringing new life into existing buildings—rather than constantly building new ones. “Don’t build. Reuse,” she says. “We should think about how we should extend the lifetimes of the buildings we have.”
Panelist Sophie Pennetier, associate director, special projects at Enclos, agrees. New buildings should also be “designed for disassembly,” she says. This means there will be easier recovery of products and materials when a building is disassembled or renovated, meaning less construction, and thus less carbon, will be produced.
Glass Magazine’s 2024 All About Glass & Metals: Guide for Architects digs into these key considerations for glass sustainability. It adapts several NGA resources on sustainability developed by volunteer industry experts.
Part 01 offers a closer look at the payback of high-performance systems and retrofits. Part 02 addresses glass Environmental Product Declarations, a key product sustainability measurement. And Part 03 digs into the opportunities and challenges of glass recycling.
Resources from the National Glass Association
- Part 01 is based on the NGA document, High-Performance Windows Can Help Save the World
- Part 02 is based on the NGA Glass Technical Bulletin, General EPD Education
- Part 03 is based on the NGA document, Window Recyclability: Circular Economy
- All three resources, along with numerous others about the sustainability and performance potential of glass, are available in full in the NGA store.
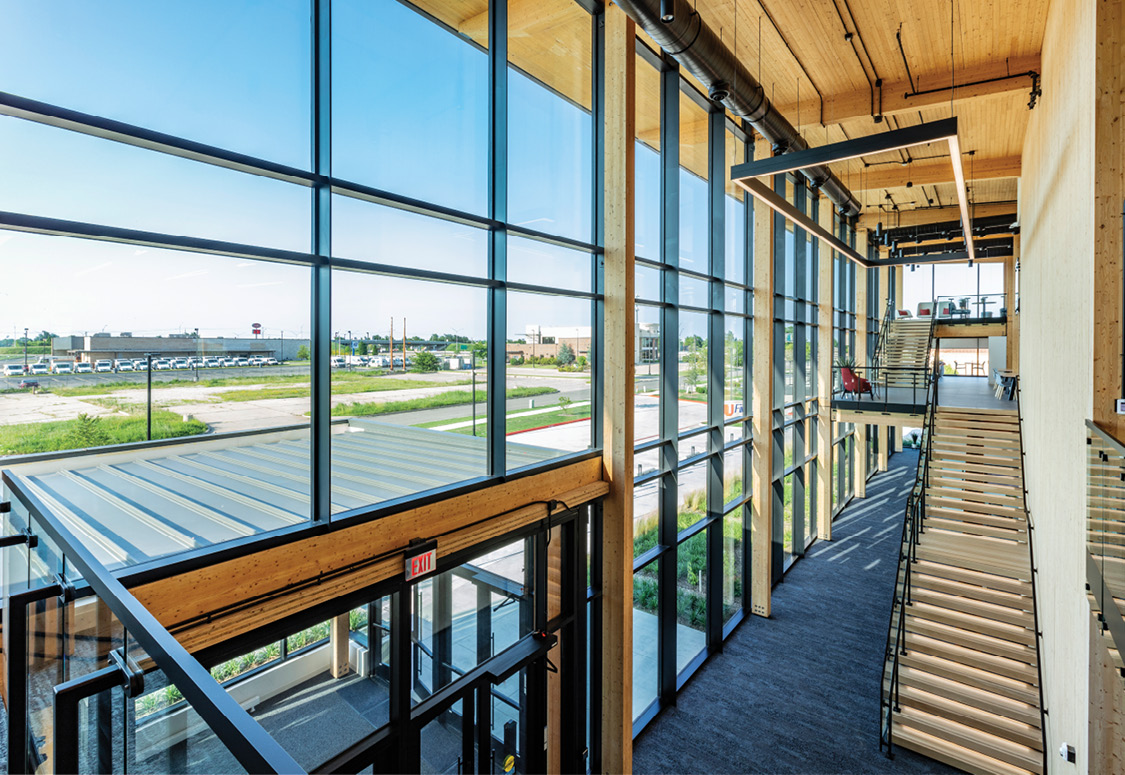
Part 01 | The Payback of High-Performance Windows and Retrofits
Higher-performing façades mean higher-performing buildings, resulting in improvements in operational carbon. Some considerations about retrofits, the payback of high-performance systems and building resiliency:
- Window retrofit is key to decarbonization.
Residential and commercial buildings are responsible for almost 40% of North America’s carbon dioxide emissions and energy usage. For example, existing buildings with inefficient windows account for about 70% of New York City emissions. Additionally, 80% of buildings that will exist in 2050 already exist today, meaning retrofits will be critical to improving operational carbon on a large scale in decades to come.
- High-performance windows are up to 80% more efficient than standard windows.
New residential windows that qualify for the Energy Star Most Efficient designation are up to 40% more efficient than new standard windows. Upgrades in window technology in the last 20 years have significantly improved heat-loss performance for residential and commercial structures.
- New windows can pay back embodied carbon in less than a year.
Glass is typically 2% to 5% of a building project’s embodied carbon. Upgrading to a more efficient glazing system will initially add some additional embodied carbon. However, in both commercial and residential installations, operational energy/carbon savings from the more efficient windows will offset that initial increase in six to 20 months in a cold climate, and thereafter, provide additional annual carbon savings.
- Decarbonization efforts should include both embodied and operational carbon.
Existing legislation targeting embodied carbon does consider the long-term benefits that glazing materials provide by mitigating annual carbon impacts through ongoing operational cost savings. Upgrading installed windows improves total building energy performance by up to 20%, improves comfort and health for occupants, and reduces operational costs and carbon emissions.
- High-performance glass is used in on-site renewable energy products.
High-performance glass is a key component in the domestic supply of solar panels and BIPV. Increased use of on-site renewable energy is critical to achieving net-zero energy and carbon targets, and will also help improve grid resiliency and U.S. energy independence.
- High-performance windows improve building resiliency.
In the event of extended power disruption, high-performance windows enhance building resiliency and maintain habitable interior temperatures for longer periods of time. Improvements allow for the downsizing of replacement mechanical systems and more effective use of funding, while increasing building resiliency in extreme weather and blackouts.
- Retrofitting buildings with high-performance windows creates job opportunities for a skilled workforce.
Installation of high-performance window products supports skilled worker job creation along with urban renewal. At the local level, changes in building performance standards requiring improvements in existing buildings are taking off, but adoption among cities is scattered. Federal-level initiatives encouraging window and building envelope upgrades, as well as lighting and mechanical system updates, would create additional manufacturing demand and related jobs.
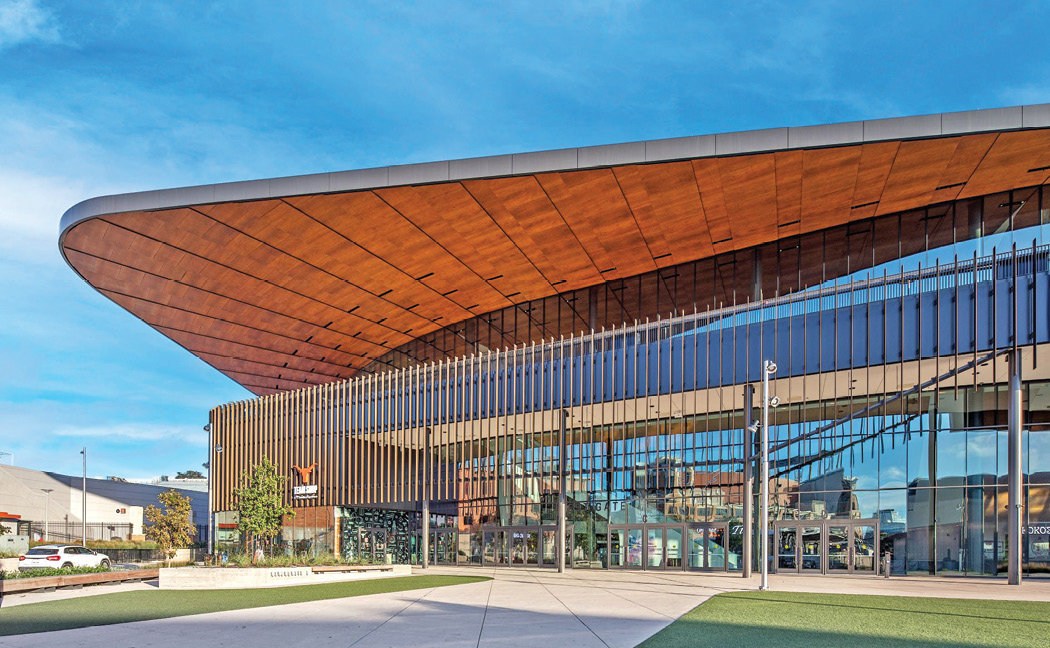
Part 2 | Glass EPDs and Caution Over Comparison
Environmental Product Declarations enable the assessment of the environmental impact of products and label them accordingly. They contain extensive and independently verified environmental data about a product, from raw material procurement to disposal. EPDs allow consumers or design professionals in the building and construction industry to make better-informed decisions about the environmental impacts of the building material products chosen for projects.
However, it has been observed in the marketplace that architectural, engineering and construction professionals are trying to compare EPD values, which is not encouraged, nor always appropriate, and could lead to misleading conclusions.
Flat glass EPD
It is important to understand how to properly read, interpret and utilize the data published in the industry-average Flat Glass EPD, developed by the NGA. This is especially critical when attempting to compare this data to manufacturer-specific flat glass EPDs, as well as the EPDs of other materials and systems.
NGA and its member companies created the industry-average Flat Glass EPD to better understand their glass products’ environmental performance from cradle-to-gate. The NGA EPD conforms to the NGA Product Category Rule for Flat Glass, published by NSF in September 2020, which describes the format and requirements for conducting life-cycle assessments and creating EPDs for flat glass products. The Flat Glass PCR requires that EPDs include the following disclaimer advising against comparisons:
“This EPD was not written to support comparative assertions. Even for similar products, differences in declared unit, use and end-of-life stage assumptions, and data quality may produce incomparable results. It is not recommended to compare EPDs with another organization, as there may be differences in methodology, assumptions, allocation methods, data quality such as variability in data sets, and results of variability in assessment software tools used.”
Caution against comparison
In general, EPDs may be used to inform and comply with the requirements of green building rating systems and legislative actions. The purpose of an EPD is to provide information on several environmental impacts of a product over the life cycle, either cradle-to-gate or cradle-to-grave.
EPDs typically rely on estimations of impacts, therefore the accuracy will differ for any particular product line and reported impact. EPDs are not meant to be comparative assertions and may not be comparable or have limited comparability. According to clause 5.5 of ISO 21930:2017:
“Comparison of construction products using an EPD shall be carried out in the context of the construction works. Consequently, comparison of the environmental performance of construction products using the EPD shall consider all the relevant information modules over the full life cycle of the products within the construction works.”
This is reinforced in “Critical Issues When Comparing Whole Building & Building Product Environmental Performance” from the MIT Concrete Sustainability Hub:
“Only compare building products in the context of a whole building. With regards to building products, unless the thermal properties, such as thermal conductance and thermal diffusivity, and envelope permeability are exactly the same, use of the products under comparison would cause different operational energy consumption.”
LEED v4.1
In acknowledgment of the challenges associated with comparing EPDs, LEED v4.1, option 2, attempts to address this by limiting comparisons to be made using an individual product EPD and demonstrating measurable improvements in different versions of that EPD. This is in contrast to LEED v4.0, which compared an EPD to an industry-average EPD. LEED v4.1 states:
“To encourage the use of products and materials for which life-cycle information is available and that have environmentally, economically and socially preferable life-cycle impacts. To reward project teams for selecting products from manufacturers who have verified improved environmental life-cycle impacts.”
Critical characteristics
EPDs are developed, particularly those per ISO 14025, with critical characteristics unique to that published document. Extreme caution should be used when comparing EPDs and the resulting global warming potentials. Significant differences may exist in some attributes, even for similar products. Comparing EPD values with differences in the characteristics below can yield large errors between the values and should be considered. When comparing EPDs, at a minimum, ensure the following are identical:
- The same Product Category Rule is used
- Declared unit (comparison of EPD results on a mass basis is insufficient; the technical performance of the product should be considered)
- System boundary (use and end-of-life stage assumptions)
- Data quality, such as variability in data sets and broad error margins in data
- EPD methodology and assumptions
- Allocation methods
- Variability in assessment software tools used
- Program manager (program operator)
- Data sources (GABI version, for example) on which assumptions are based
- Manufacturer-specific versus industry-wide
- Facility-specific versus multiple facilities
- Suppliers/supply chain
- Age of the EPD
Part 3 | Glass Recycling Opportunities and Challenges
Higher recycled material content is a key element for future decarbonization efforts for the glass industry.
Glass can be infinitely recycled in the flat glass and bottling operations, so continued reuse further supports the glass industry, supports a circular economy, and reduces waste and landfill.
These benefits drive material choice decisions, for example, using glass containers instead of less recyclable materials such as single-use plastics.
Glass recycled materials can be used in various industries, from recycling back into the melt furnace to make new windows, glass containers, road grade, fiberglass, reflective highway paint, landscaping products, countertops and coastal restoration materials.
Recycled glass is valuable
Recycled glass, or cullet, helps reduce the energy and emission burdens on glass manufacturing by:
- Reducing the need for raw material mining.
- Reducing trucking and related emissions, as making 1,000 tons of glass requires 1,000 tons of cullet or about 1,200 tons of raw material, or “batch.”
- Reducing furnace emissions. Batch material and firing fuels both off-gas during the glass-making process. Increased cullet usage significantly reduces the emissions from production.
- Reducing gas usage. Cullet is easier to melt than batch, so lower furnace fuel is required.
- Reducing global warming potential of glass, as less energy is needed to make glass when cullet is available.
Recycling glass supports domestic supply and workforce
- Cullet should be considered a viable, reusable and sustainable domestic material supply chain.
- The glass recycling industry creates jobs and tax benefits.
Glass recycling is challenging
- Economics and glass quality requirements present challenges for glass recycling.
- Freight costs typically drive recycling decisions. Long hauls of heavy products often make recycling a cost challenge.
- Sorting and cleaning of cullet for certain applications can be expensive. In contrast, landfill costs are generally inexpensive in the United States.
- Contamination from even trace amounts of certain elements like nickel and aluminum can dramatically impact glass quality.