Building Efficiency
Metal companies adapt their systems for less labor and greater sustainability
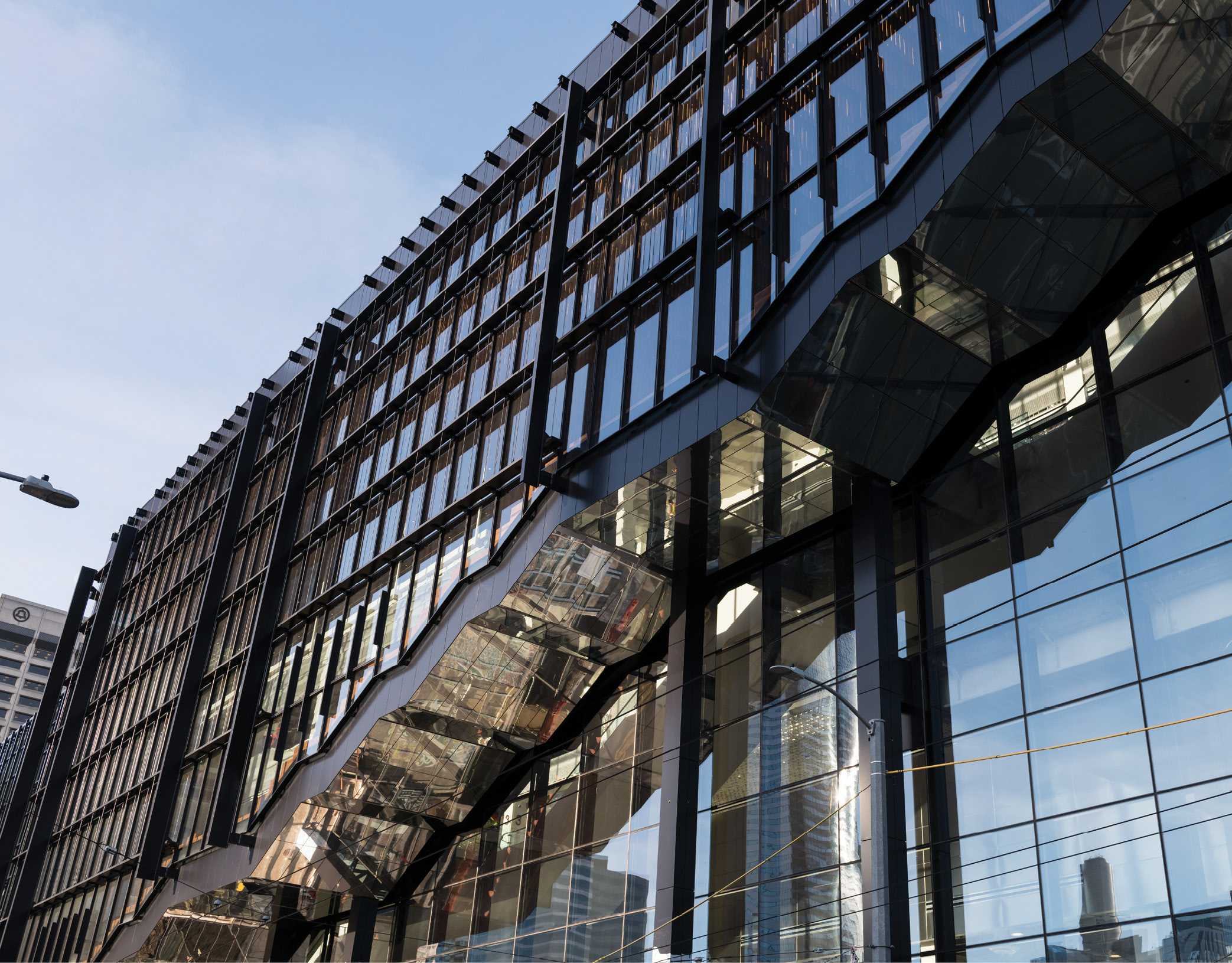
Above: One of the first vertical convention centers in North America, the 15-story Seattle Convention Center Summit building’s curtain wall features Technoform building envelope products aimed at fulfilling the project’s sustainability goals. Fabricator CareyGlass International selected Technoform’s plastic hybrid stainless steel warm-edge spacer as its edge seal solution. The aluminum-framed curtain wall, manufactured and installed by Enclos, also integrates Technoform’s polyamide thermal barriers throughout the fenestration assembly. Inside the center, visitors and staff are treated to expansive views and abundant natural light from the large atriums to “The Hillclimb” glass-enclosed staircase, into the exhibit halls, and up to the grand ballroom. Photo courtesy of Technoform.
2023 has been a slightly more stable one for glass and metal companies, say leaders in the industry. Supply chains have calmed down, even though inflation and interest rates remain a question mark. “It feels like we finally have control of the future a little bit more. Before, it felt like we were just kind of hamstrung,” says Josh Wignall, director of commercial sales and marketing, Quaker Windows & Doors.
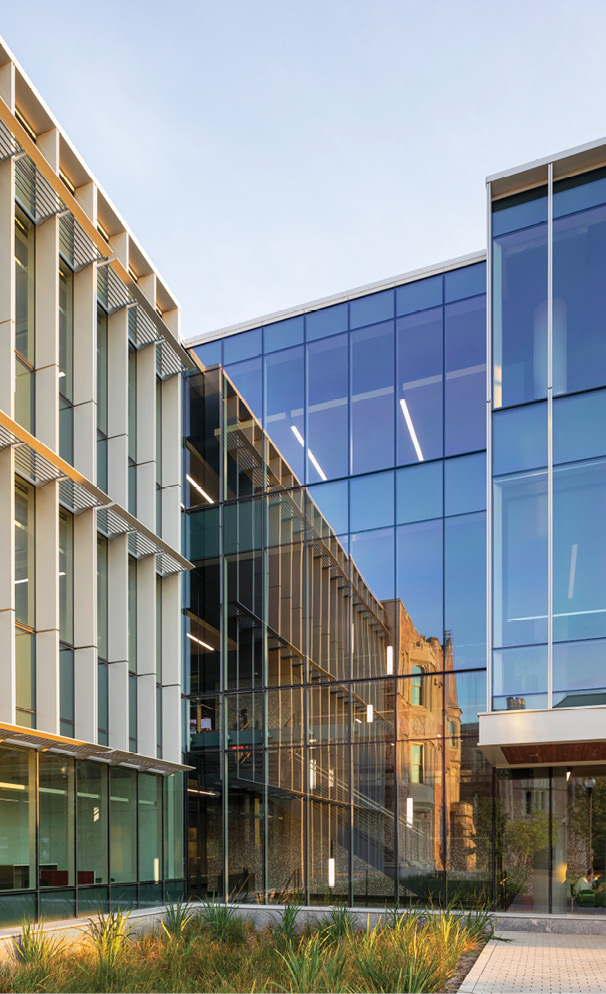
While most companies voiced a sense of cautious optimism and a return to the business of building, what has not changed is the difficulty of finding labor. Across the board, labor is expensive, and there’s not enough of it. “I still hear from multiple industries that companies are still struggling to find enough staffing to do the job. It’s gotten better, but it’s not back to where it was pre-COVID,” says Mary Avery, vice president of marketing, Tubelite Inc.
High labor costs may be pushing the adoption of some metal systems, says Zeke Miller, president, MillerClapperton, which fabricates and supplies metal composite material and plate aluminum panels, among other building products. Miller sees greater adoption of the company’s products in lieu of eaves, stucco or lower-density fiber cement, likely due to labor costs.
“Because all those products are still very labor intensive. And labor is just out of control right now.”
Prefab systems offer speed and quality control, but require space and transportation
Lack of available, skilled labor is also fueling a continued rise in prefabricated and modular systems, say industry representatives, though adoption can depend on the company’s capacity.
Prefabricated systems can be used as an umbrella term to refer to a range of building systems that are fabricated or constructed in a manufacturing environment before being shipped to the jobsite. Unitized systems often refer to a façade system or curtain wall that is pre-glazed or has windows installed. Modular systems describe a container-type system. Reps for Kawneer say they see modular building happening more on smaller projects, such as hotels, where room and floor layouts are fairly identical.
Prefabricated options offer several advantages for project completion and can accelerate production timelines. “A main advantage is just construction speed,” says MillerClapperton’s Miller. “You can dry-in a building much faster, literally an entire floor in a day [using prefabricated systems], whereas with traditional stick-built construction, it could take a week, two weeks or even longer to dry-in a floor. Drying-in early allows the interior trades to start earlier.”
Prefabrication in the factory or shop can reduce labor needs and increase quality in a more controlled, automated environment. “Factory fabrication requires less people and involves more automated and lifting equipment. In a prefab situation, you’re setting the units, locking them in place and then can move on, versus having to go unit by unit and dropping them in [like you would in the field]. The workforce required to do that in the field is much more expensive than what you must do for modular or unitized systems,” says Quaker’s Wignall.
While beneficial for the jobsite, considerations remain for implementing prefab in the shop, especially the space required. “Shop-glazed or unitized units take up considerably more space than shipping fabricated parts,” says John Trainor, general manager, AGS Inc. Transportation of systems is also a major consideration, he says. “How do you bunk the units? Load and unload the bunks? How many units can you fit on a truck?”
C.R. Laurence’s Mark Suehiro, technical director, product group sales, architectural hardware, says companies can think strategically about their goals in bringing fabrication in-house. “For shops that want the flexibility to fabricate on-site and eliminate the possibility of manufacturing delays, the modular approach works great. Other shops want to focus on the install, using completed systems built-to-spec, which makes the unitized approach optimal.”
Interest grows in circularity, embodied carbon and recycling
Sustainability initiatives continue to transform markets, say industry reps. Code changes especially have accelerated more stringent performance requirements in recent years. “It used to be the industry had a sell time on systems of multiple years,” says Tubelite’s Avery. “Now codes change quite often.”
Some of the resulting energy and thermal efficiency code changes have had significant impacts. “We are seeing customers designing completely new systems to address more stringent energy codes, especially in Canada, but also in the Northeast and Northwest U.S. They are utilizing deeper thermal barriers—moving from approximately 28 millimeters to approximately 50 mm—and lower thermal conductivity materials, such as low lambda polyamide for thermal barrier products,” says Chad Ricker, general manager, Technoform.
Beyond product energy performance, there is an increasing interest in sustainability throughout the manufacturing process. “In building design, the focus is definitely shifting to total embodied carbon during the building’s sourcing, construction and operation,” says YKK AP’s Derick Clutchey, director of branch sales.
Kawneer reps say they also see interest in material transparency, environmental product declarations from the architectural community and growth of the retrofit market. “A lot of focus now is on how to reskin existing buildings, to make those buildings more energy efficient without necessarily knocking them down,” says Chris Giovannielli, director of global product management, Kawneer.
An interest in the reuse and recycling of building materials also continues to expand. Giovannielli points out that better waste management and recycling is a byproduct of factory prefabrication. “If you think about how buildings and homes have been built over the last 50 to 60 years, there’s a dumpster at the jobsite, and then all the cut-offs always wind up in a dumpster which goes to a landfill. … What we’re beginning to see more of now is how we can recycle more of these materials,” he says.
Despite the increasing interest in manufacturing and specifying more carbon-neutral systems, MillerClapperton’s Miller says he still sees energy-efficient solutions, such as continuous insulation, dropped from projects when the cost gets too high. “The architects always make a valiant attempt to get the proper [continuous insulation] designed into the project, but it’s usually the first thing to be value-engineered out of a project. Everybody says it’s an absolute requirement until you get the price, then all of a sudden, they can live without it.”
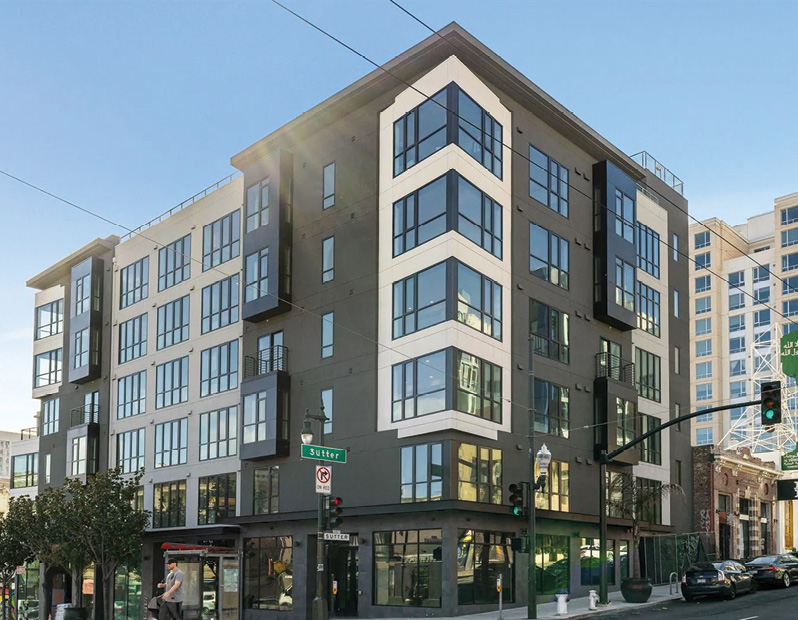
Remodeling and institutional building remain strong
Most industry reps report a slowing commercial sector. “The commercial segment and multi-family housing market has slowed in recent months, so cost-effective solutions are, and will become, more prominent in this space as budgets tighten,” says Matt Syring, director of project planning, Sightline Commercial Solutions. YKK AP’s Clutchey says growth in commercial and multi-family is also very regional. “Larger markets like Atlanta, Boston, Houston and Los Angeles remain strong,” he says.
Institutional building, however, is growing. Many reps said health care continues to be a strong segment. “Trends seem to be going to those freestanding emergency departments, smaller facilities that do 75% of everything, rather than a larger facility that does everything,” says MillerClapperton’s Miller.
University and K-12 school building is also a strong sector. For university campus building, Kawneer’s Giovannielli says he’s seen projects mixing retail and dormitories to “create an experience” for students. “Universities are creating more of a ‘back home’ feel [with these new buildings] versus a five-story building that has punched-out little windows,” which used to be common.
After pause in interest rate hikes, companies plan ahead
Interest rates have been a major concern this year, with July marking the 11th interest rate increase by the Federal Reserve since March 2022. As of this writing, the Federal Reserve has not raised interest rates again, but may do so by the end of 2023.
For the most part, interest reps were fairly neutral about inflation and interest rate increases. Still, the possibility of a changing financial landscape is leading to project pauses for larger, more expensive projects, says Tubelite’s Avery. “Under any type of uncertainty, there’s a bit of a delay. And there’s some concerns around some banking situations right now.”
Supply chain snarls remain mostly in the past, but companies have focused on securing vendor and supplier relationships to ensure resiliency. “Our procurement team continues to diversify our suppliers, as needed, to ensure we continue to provide our products to market in a timely manner. We have also enhanced our risk exposure and management strategies when it comes to our supply chain partners,” says YKK AP’s Clutchey.