Next-Level Curtain Wall Performance Solutions
High-performance fenestration systems include low-conductivity pressure plate systems to help meet energy code needs
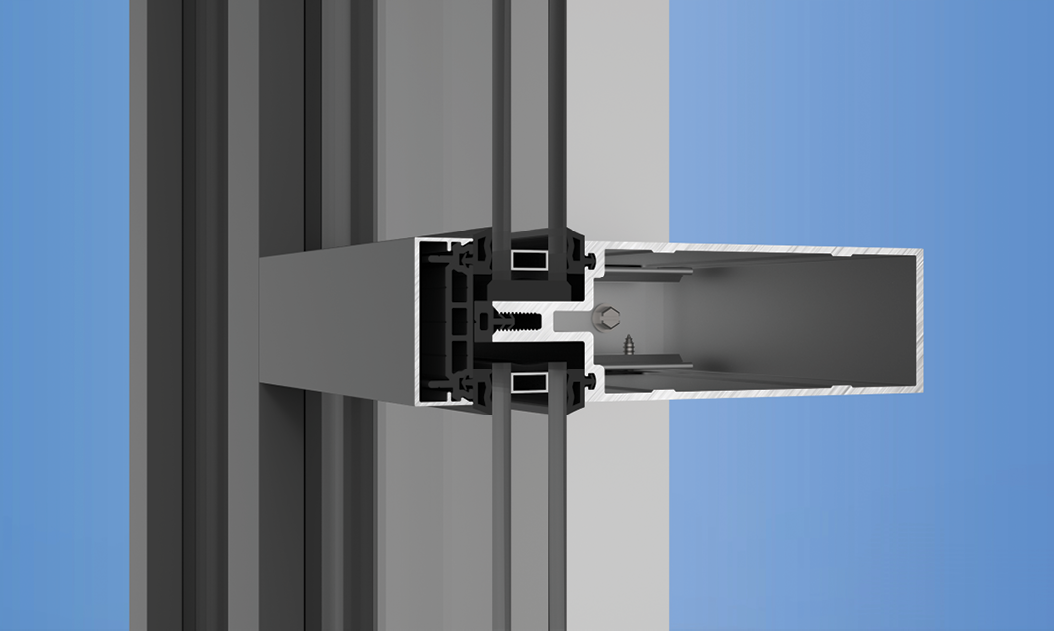
Above: Outside glazed pressure wall system with polyamide pressure plates. Photo by YKK AP America.

Fenestration products play an important role in commercial buildings, beyond providing good aesthetics. Daylighting, thermal comfort and air infiltration can be positively impacted by high-quality, high-performance curtain wall systems. However, poor system performance can reduce thermal comfort and increase the costs to cool or heat a building by transferring all energy directly to the inside or outside, depending on the season.
Commercial building codes are continuing their progress toward increasing the thermal efficiency of the façade. Additionally, the International Energy Conservation Code and ASHRAE 90.1 Energy Standard for Sites and Buildings are now pushing to achieve net-zero energy by 2030-31. Building codes constantly lower the prescriptive values for fenestration U-factor with the 2024 IECC lowering U-factor for fixed fenestration to 0.25 British thermal unit per hour per square foot per degree Fahrenheit (Btu/hr*ft²*°F) in climate zone 8, 0.34 Btu/hr*ft²*°F in zones 4 and 5, and 0.38 Btu/hr*ft²*°F in zone 3.
Lower prescriptive U-factors encourage fenestration manufacturers to explore new solutions that can give them a competitive edge and increase system performance. Traditionally, manufacturers incorporated high-performance glass technology to meet stringent energy requirements, but glass changes can be expensive. Moving from a double-pane system to a triple-glazed increases the costs and complexity of a system. Glass is also only one part of the entire system, and a simple change to the frame could help elevate a poor or mediocre performing product into a high-performance system.
Typical curtain wall systems utilize aluminum pressure plates, which have a very high thermal conductance and can affect condensation values. Replacing aluminum pressure plates with polyamide pressure plates can greatly increase the performance of a system as polyamide is 500 times more insulating than aluminum. Additionally, polyamide pressure plates can increase condensation resistance, which allows for higher humidity levels and more comfort in buildings.
Some tested products have achieved approximately 24% better U-factor and 20% higher condensation resistance values when replacing aluminum pressure plates with polyamide pressure plates.
Fiberglass pressure plates also offer an alternative material to help increase thermal performance of a system. Fiberglass offers rigid products with tight tolerances and can be swapped with little change to original system. Custom fiberglass pressure plate shapes also can be created to fit a specific system requirement. However, fiberglass profiles can be more difficult to machine and fabricate because special saws and ventilators to ensure manufacturers do not have negative reactions to the cut fiber typically are required. In contrast, polyamide pressure plates do not require any special fabrication or safety equipment for processing and custom shapes are available.
High-performance fenestration systems can be achieved utilizing a variety of verified materials, glass and spacers to help manufacturers meet the energy code needs of tomorrow.