Next Step in VIG: Planning for Growth
VIG is expanding in performance
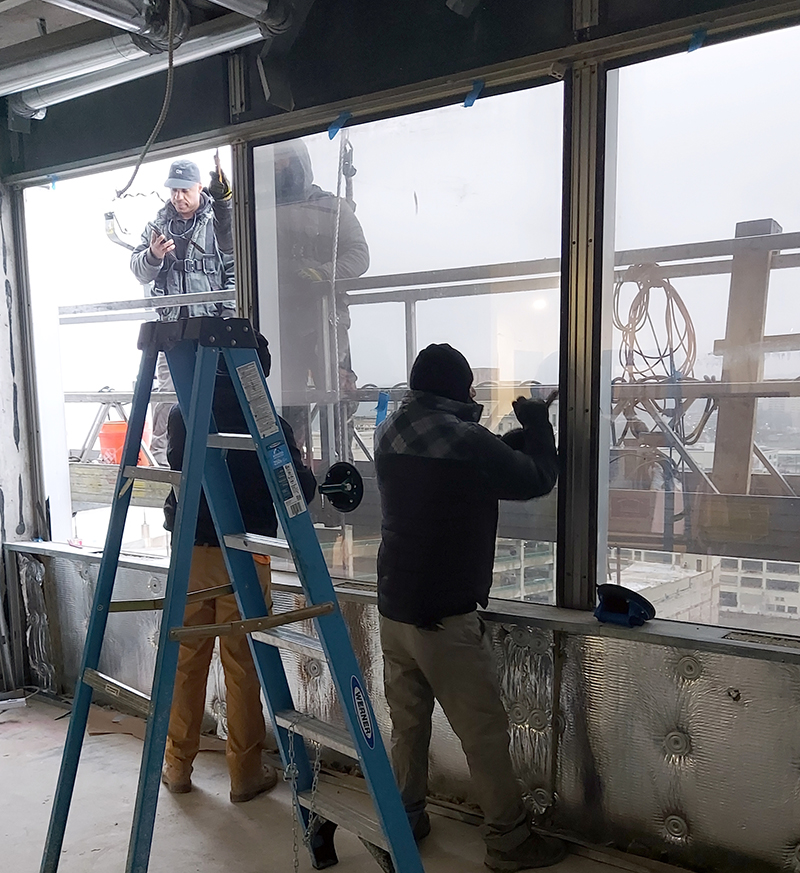
Vacuum insulating glazing, or VIG, is a next-generation glass product. Like an insulating glass unit, the system is comprised of two monolithic lites of flat glass; in VIG, they are separated by pillars or standoffs, and edge-sealed, with the air vacuumed out through a pump-out port.
But the technology is not new, emphasizes Dave Cooper, president and chief technical officer, VacuumGlass LLC, whose company sells both VIG products and the fabrication equipment to make them.
“[VIG has] been around for quite a while. But like many things, our side of the Atlantic or Pacific is slow to adapt and change,” says Cooper. His company did a survey of global VIG manufacturers; currently almost 80% of production is in China, though capacity does exist elsewhere in Asia and Europe, he says.
Imports of VIG to North America have increased in the past few years. Cooper’s company has set up exclusivities with six different manufacturers from China. Vitro Architectural Glass, through its partnership with LandGlass, also supplies VIG to the North American market.
“VIG 3.5” features better performance, tempering and longevity. There have been several recent advances in the technology, says Cooper. Compared to where the technology was when it was invented decades ago, he says today’s VIG is “version 3.5.”
Recent advancements
- No leaded frit for edge-sealing. While VIG was traditionally produced with leaded frit as the edge-seal material, some customers did not prefer this due to sustainability considerations, says Cooper. His company can now produce lead-free product, though it’s still more expensive and more difficult to manufacture.
- Elimination of pump-out port. A pump-out port is the cavity used to pump air out of the VIG unit, creating the vacuum. That can be considered a disadvantage aesthetically, says Cooper, since the small circle of the port draws the eye. It can also be accidentally knocked off during maintenance (like window washing), which reduces performance. Now, a couple manufacturers have been able to eliminate this port, Cooper says.
- Edge-grinding to prevent breakage. Crisp, clean edges on the glass aid in minimizing potential breakage at the edge, Cooper says, which is ideal for VIG as it’s a more expensive product.
- New pillar technology. While the pillars, which hold the two lites of glass apart, are traditionally made of metal like stainless steel, manufacturers are experimenting with different types of materials that offer less conductivity. Additionally, companies are experimenting with printing the pillars directly onto the glass.
- Jumbo sizes. Like all glass systems, the market is demanding big sizes. Cooper says his company is able to manufacture units up to 170 inches wide.
- Fully tempered, including at the edge. One of the final steps of VIG assembly is edge sealing, which requires melting the edge material onto the tempered glass. Unfortunately, this can potentially de-temper glass that is already tempered, says Cooper. However, many companies have been able to experiment with sealing quickly at low temperatures using proprietary materials, says Cooper, to create a product that can pass a safety glazing standard.
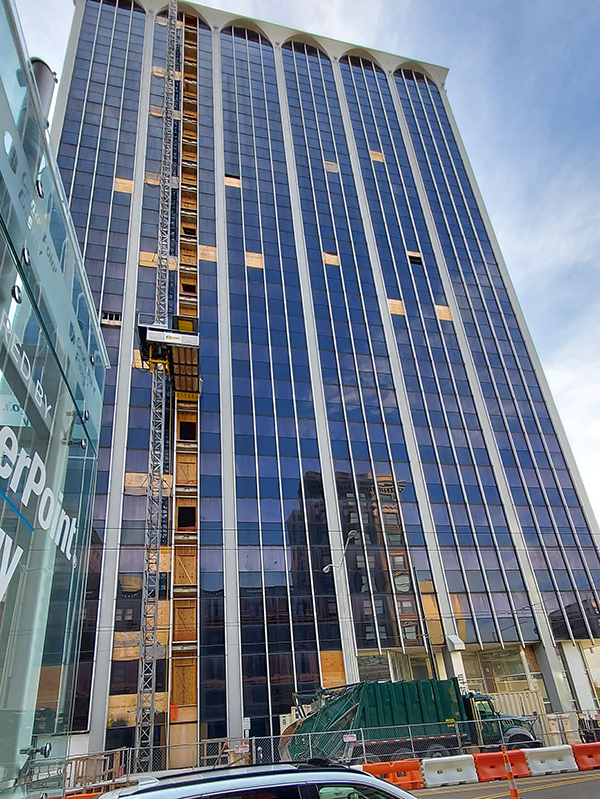
Historic Grant-Deneau retrofit represents largest North American use of VIG
VacuumGlass is supplying VIG systems to a retrofit of Grant-Deneau tower, a 22-story building located in Dayton, Ohio. Cooper says the project represents the largest use of VIG in North America.
The historic tower was built in 1968 using PPG monolithic solar gray glass. Previous owner Premier Health left the building due to the high costs of running it, says Cooper. The new owner Windsor Companies, in renovating the tower to become a mixed-use building, decided to implement VIG. The decision allowed the construction team to match the existing architectural aesthetic says Cooper, and to take advantage of the 17D tax credit, a recent incentive that rewards building renovations that improve energy efficiency.
The building owner had a building analysis completed and was able to move away from conventional HVAC system replacement, due to the use of VIG, says Cooper. The use of VIG high-efficiency glazing to replace the R1 monolithic glass enabled the building to go to an electrified efficient heat pump system.
Where is VIG going, and what’s needed for growth?
The Grant-Deneau tower, and its potential to make VIG more interesting to building owners, represents an inflection point for the material, says Cooper. “If this is the stage where we're starting to see VIG incorporated into larger and larger buildings, both new construction and retrofit, that means that we won't be able to import this [product] forever,” Cooper says.
According to a study completed by Cooper’s business, Fenestration Consulting Services, of the market segments that could adopt VIG—which includes refrigeration, commercial architectural and residential architectural—19% of those segments are currently ready to adopt the new technology. And to actually supply VIG to that portion of the market would require 250 VIG lines, he says; currently North America has none.
“We're like we were in the early days of insulating glass where people were bringing in equipment from Europe,” says Cooper. “We just need the equipment here to start producing the product.”
Fabricators interested in purchasing equipment continue to have questions about product demand and how the market is developing, as well as the capital investment required; VIG production equipment is still more expensive than other IG production equipment. As with other systems, as market adoption increases, costs will drop, says Cooper.
As for the market factors driving VIG adoption, they include codes, northern latitude standard requirements and energy zone requirements, though the “big driver” right now is costs, says Cooper. Codes are driving some adoption he says, but even if they started requiring more implementation, the market could not currently supply it. With regional codes in California, Massachusetts, New York and Colorado pushing higher energy performance, VIG may still find further adoption. “VIG will take you to that [standard], to that level and beyond. So, you've got a future-proof product.”