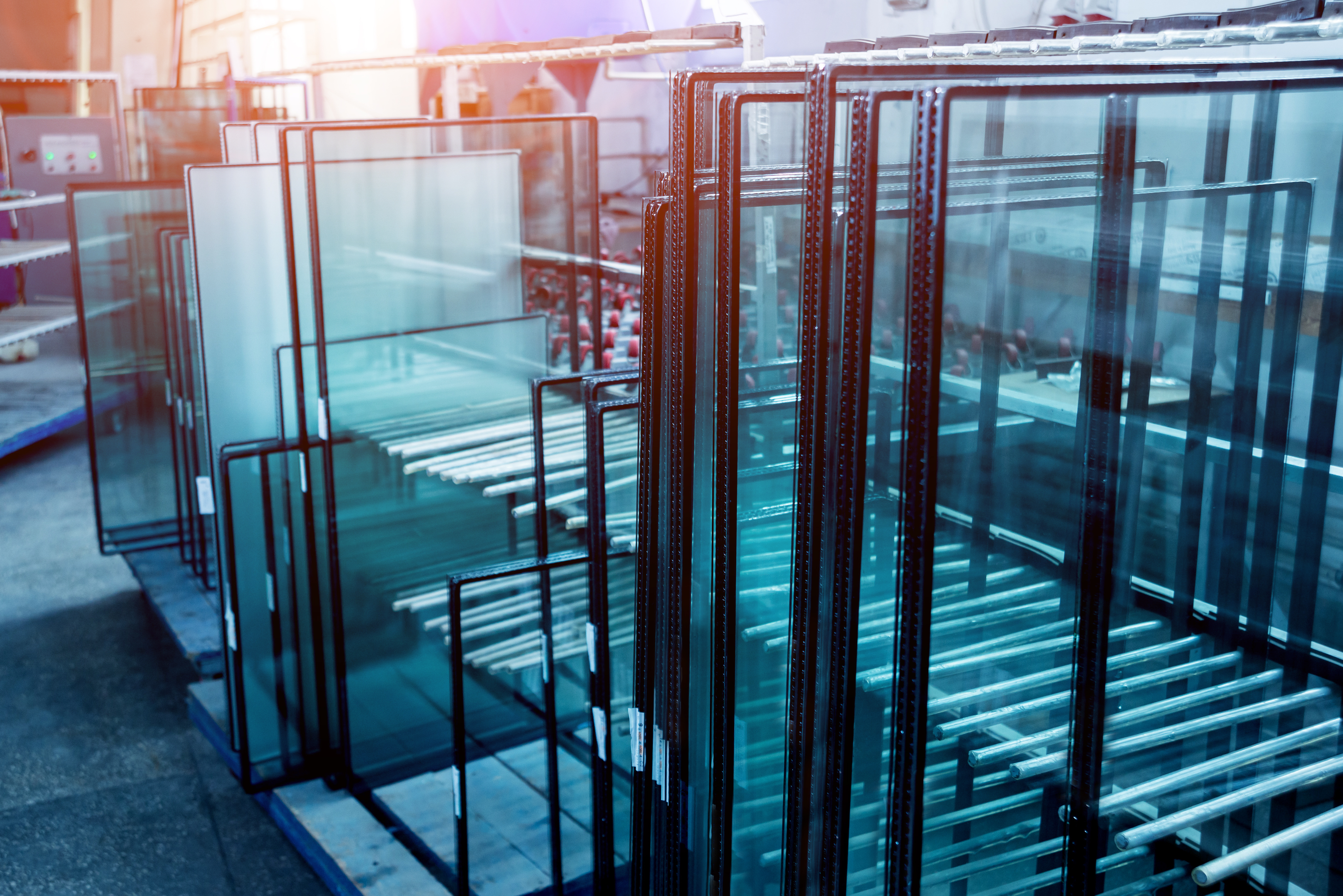
Insulating glass units are dynamic assemblies. The glass panes on either side of the central cavity can bow in or out as ambient air pressure increases or decreases due to the elevation of the installation site versus the manufacturing location, passing high- or low-pressure weather systems, or changes in temperature. Such glass deflection can cause failure of edge seals and spacers over time, and in extreme cases, glass breakage.
This is a complex issue, as many variables can affect the cavity pressure, including glass type and thickness, glass area, aspect ratio, cavity width, sealant and spacer selection, and spacer size. To forestall problems, IG units can be provided with a compensation system that permits regulation of internal gas pressure.
There are several methods for compensating the IG unit cavity, which are described in detail in the newly published IGMA TM-3200 manual, Design Considerations for IG Unit Cavity Pressure Compensation.
Methods used to regulate internal pressure
Reseal holes
Holes into the sealed cavity, created either in the field or at the factory, are permanently sealed in the field after pressure compensation is accomplished.
Insert tubes
A capillary tube is inserted in an IG unit during fabrication to control unit internal pressure during shipping and/or during in-service use. Typically, these are small-diameter aluminum or stainless-steel tubes that allow slow pressure equalization of the IG unit cavity. (More details are covered in a separate publication, TB-1601/95 (14), Guidelines for Capillary Tubes.) Note that capillary tubes are not recommended for use in gas-filled IG units.
Apply post-fabrication valves
This option usually takes the form of a one-way valve applied post-fabrication (often at the installation site) that can be mechanically depressed under a specific pressure differential load to adjust the pressure in the cavity. After venting, a spring mechanism closes the valve.
Adjust pressure
The manual outlines several options for adjusting pressure:
- Desiccant adsorption. This technique typically involves the adsorption of a sacrificial gas, mixed into the insulating gas at the time of filling, onto a desiccant material added to the cavity to reduce cavity pressure. This allows sealing at atmospheric pressure, without the need to puncture the spacer or glass for pressure adjustment after sealing.
- Pre-inflating/pre-deflating. Pre-inflating and pre-deflating is accomplished by removing or injecting gas to increase or decrease the volume by a specific amount to compensate for the expected expansion or contraction of the gas. This method may not work for certain IG unit constructions, due to increased stress on the seal and glass.
- Temperature manipulation. The entire unit is heated or cooled prior to sealing and/or gas filling, thereby impacting the gas volume. This is an easy way to implement the process and is predictable, but there are some drawbacks as well.
Use bladder relief system
A bladder relief system consists of an external flexible container connected to the IG unit cavity via a tube. The bladder inflates or deflates as necessary to allow the IG unit cavity to exhale and inhale as the unit is transported and/or as temperature and pressures change throughout the life of the IG unit. It can be used for a single IG unit or in parallel with multiple IG units. A bladder relief system is effective, but introduces numerous issues as discussed in the manual.
Resources
The TM-3200 manual offers advantages and disadvantages of the above methods, as well as manufacturing and workmanship considerations, storage and handling, implications for glazing (installation limitations, recommendations, etc.), and IG design considerations for environmental conditions.
Included for quick reference is a table summarizing the advantages and disadvantages of the above listed pressure equalization methods, allowing easy comparison and choice of which to use. Commercially available software programs that can address the aforementioned variables and predict the glass deflection are listed in the manual.
Learn more at FGIAonline.org/store.