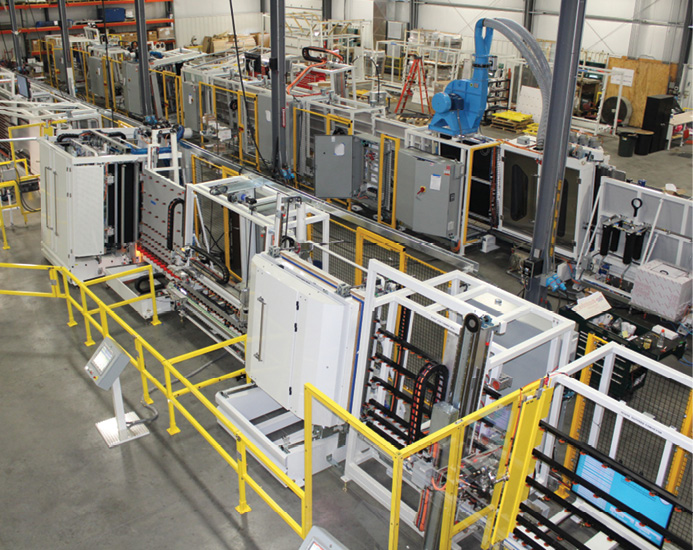
Pictured: The Erdman® High Speed Dura line produces IG vertically in a fashion that nearly doubles the speed of traditional vertical lines—a first for vertical automation for the single-seal IG market. Vertical production eliminates the need to tip a unit up to four times in the production sequence, which saves time, eliminates injury potential, qualifies more operators for service and minimizes breakage.
Challenge
Insulating glass manufacturers expect more out of their IG production equipment, including speed and benefits such as reduced floor space and labor, and a higher-quality product.
Solution
The Erdman High Speed Dura line produces IG at a rate nearly twice as fast as a “traditional” IG line. Total labor for the Dura High Speed line is three to four operators per up to 1,200+ units per shift.
Case in Point
Kyle Hawthorn, Mathews Brothers Co., shares how the Erdman® High Speed Dura line changed production:
“The Automated Parallel Process Duralite IG line has given us a huge advantage in an area with a very low unemployment rate. We have been able to shift a significant amount of labor into more critical thinking tasks. We can accomplish what we do on one of our standard goal post lines (12 employees, 10-hour shift) with four employees in an 8-hour shift on the Erdman Automation line. Additionally, SAM, or the ‘Swiggle Application Machine,’ which automatically applies the Duralite, also lowers the amount of soft tissue wrist injuries by decreasing repetitive tasks needed to be done by employees.
“The inkjet printer allows us to stamp the spacer system as opposed to etching the glass with a laser or sand. This allows us to greatly minimize any obstructions to the sight line or view of the windowpanes. And, the argon filling chambers have lowered our costs as they fill more efficiently than any of our previous methods.
The unique industry heating methods allow for immediate sealing of the units, which increases our quality control and leads to a better product for our customers. The final press has an application of even pressure, as an alternative to the standard tapered roll press, which we feel adds to the quality of the units.”