2020 Industry Trends | Part 3 | Equipment & Automation
Machinery reaches a new level of maturity to further meet demands for automation, flexibility and efficiency
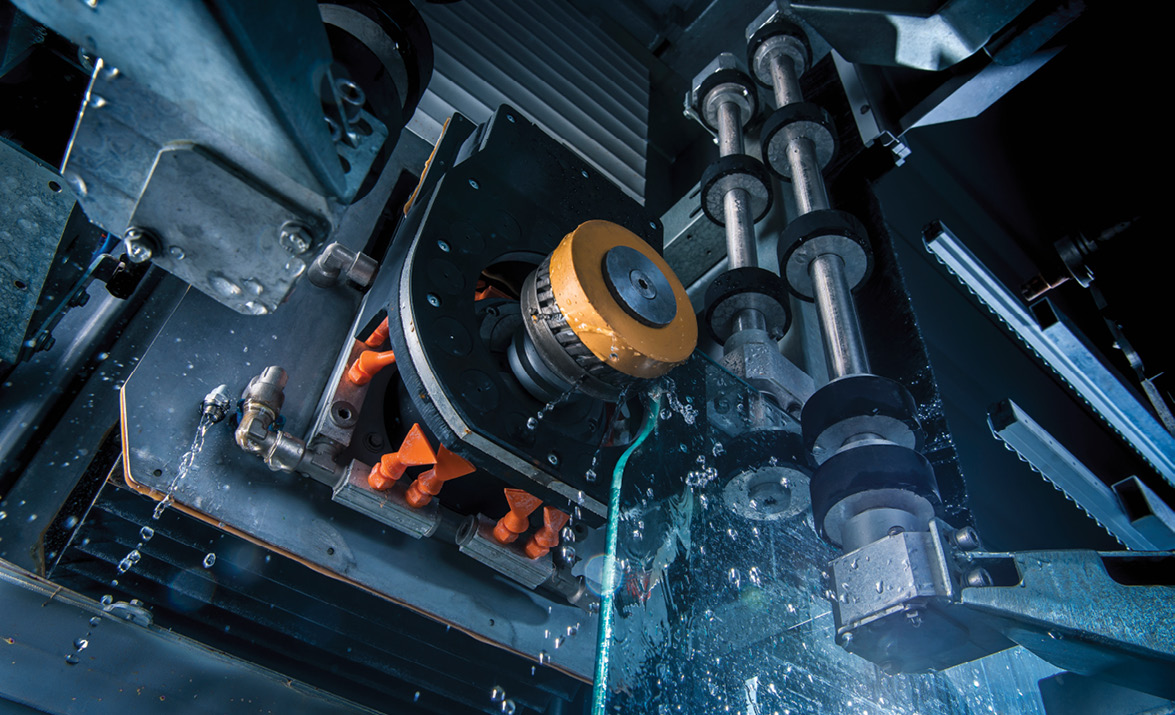
Machinery has gained more time in the spotlight in recent years thanks to automation and its increasing capabilities, especially in light of the industry’s chronic workforce shortage. Since the coronavirus pandemic altered the world earlier this year, advanced machinery solutions are even more important for manufacturers, as they strive to keep up with demand while adhering to social distancing and other safety measures to protect their human bandwidth.
The product category has spent the past years in rapid development. Today’s factories are hyper-focused on high-performing machinery that delivers accurate results and has the flexibility to produce exactly what their customers request.
“The trend is to consolidate well-known technologies and turn them into direct revenue for the final user,” say Gino S. Gramaglia, sales manager, and Joe Gates, technical services manager, Lattuada North America. “There is very little space for ‘nice-but-useless’ novelties; the feeling is the market is becoming more ‘mature’ regarding machinery. All those solutions (automation solution, robotics) that can effectively reduce dependability on human skills are welcome in glass processors of almost every size, given that it is becoming more and more difficult to find qualified operators, and processors are growing reluctant in investing in training.”
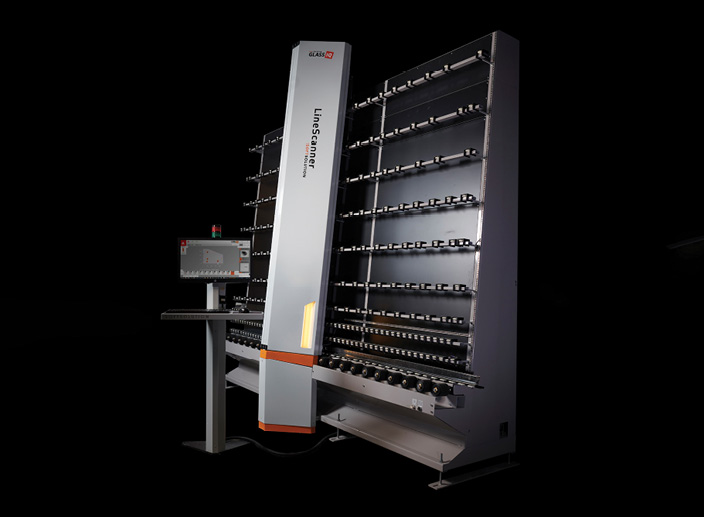
Automation and interconnectivity
Factories across the world are evolving to become smarter, more connected facilities where glancing at a single user dashboard can tell an operator the status of nearly any item processing at a given moment.
“Currently, there is much more focus on the integration of work cells on the shop floor to eliminate islands of automation,” says Dave Miller, group manager – business development executive at FeneTech. “In many cases, this automation was first designed to reduce manual movement of glass for various reasons, including employee safety and reduction of breakage and scratching. Today’s factory is much more integrated. Tighter communication between systems and well-defined workflow rules are becoming even more critical.”
Nate Huffman, president of Softsolution North America, says nearly all equipment is designed to handle the Internet of Things and Industry 4.0. “Automation seems to be the driving force in most of the technological advancements we see on the floor,” he says. “The future of IoT will hopefully start tying together all the different machinery that can be found on the shop floor. The more communication between the production islands in the process, the better feedback and traceability the manufacturers will be able to see in real time.”
Josh Rudd, sales executive at A+W Software, says it’s imperative to be able to tie machines together for greatest efficacy. Without proper supportive software that feeds machinery the proper data and sequence, he says, a machine won’t be able to live up to its full capability. “Technology can maximize a machine or a particular set of flows—different operations from machine to machine and through logistics.”
“We maintain that any job that can be automated must be automated,” says Michael Spellman, president, IGE Solutions. “We have now connected all the custom fabrication work areas to islands of automation, and from islands of automation, to full custom glass fabrication facilities.”
Automation also presents an opportunity for companies to set themselves up for long-term success and stability. “The need for automation may be depressed slightly in the short term due to the unemployment numbers, but in the long run it will be critical to compete with foreign labor prices and also the next pandemic,” says Morgan Donohue, president of Erdman Automation. “Those who are the most automated will have the advantage over the competition.”
“Customer requirements and markets are rapidly changing, which is why products and services will become more ‘digital’ and will be brought to the market faster in the future,” says Claudia Guschlbauer, head of corporate communications and marketing, Lisec. “Companies will be required to adapt faster and to continuously re-think their business models. Satisfying customer needs will be a more dynamic and creative process in the future. Anyone who fails to catch the digitalization train will lose out in the long run.”
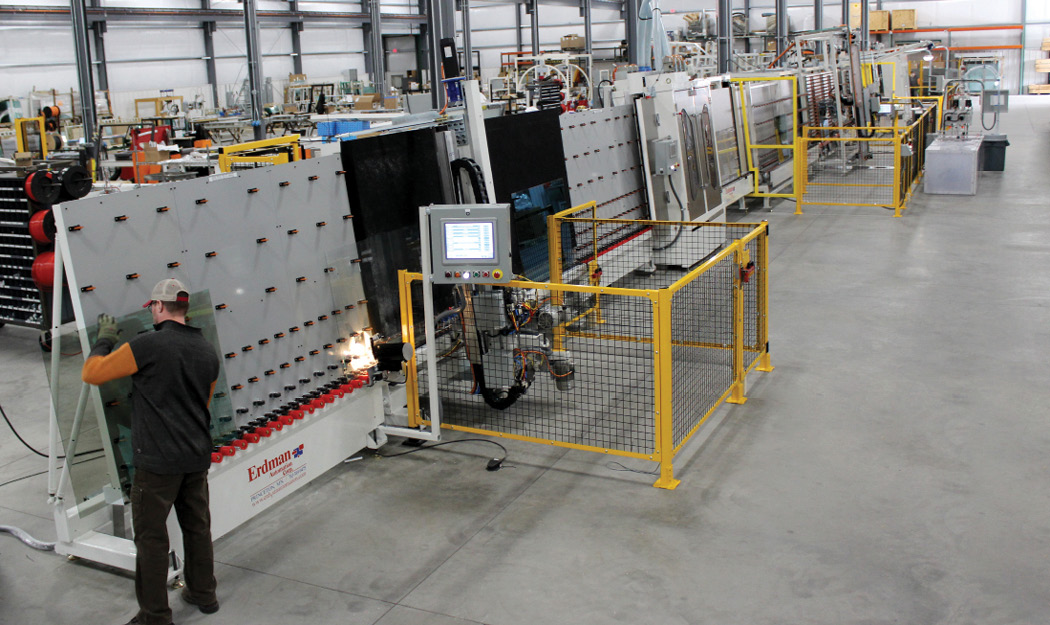
Flexibility
More machinery manufacturers have requests for machines that can switch gears if need be. “We have recently seen a push from prospective buyers for equipment that is more flexible (can produce a wide variety of parts) and more automated,” says Derek Burkholder, vice president of sales/engineering, Casso Solar Technologies. “Historically, we have seen most U.S. customers make cost-based decisions when choosing a supplier, but the current trend is toward making capability-based decisions.”
“Even larger companies want to be ready to deliver big, medium but also small batches of glass if the added value to them is worth the effort,” say Gramaglia and Gates.
Mike Synon, president and CEO of HHH Tempering, has seen tempering and laminating striving for bigger sizes and as such sees furnaces shift from 60 inches wide to 130- to 150-inch-wide furnaces. “Because the glass is so large, there is more automation on the fabrication side,” he explains. “They try to grind, polish and drill holes without people touching it.” He also references architects driving the trend of bigger, longer, wider pieces of glass, sometimes up to 20 feet.
Digital printing also is gaining momentum in its popularity and offerings. Faster, more flexible machines allow for a wider range of ink colors and enable job switching with minimal setup time, according to Yariv Ninyo, head of business development at Dip-Tech. Ink portfolios also are expanding to include precious metal inks like gold and rose gold, and conductive ink for automotive and architecture applications.
“We also notice a growing demand for a full, 360 solution rather than just the actual printers, meaning companies are required to provide an enveloping offer—machine, ink, relevant software and special services that support the machine and its production,” says Ninyo, who anticipates single-pass machines that allow for a high-quality print combined with fast, mass production capabilities coming to fruition.
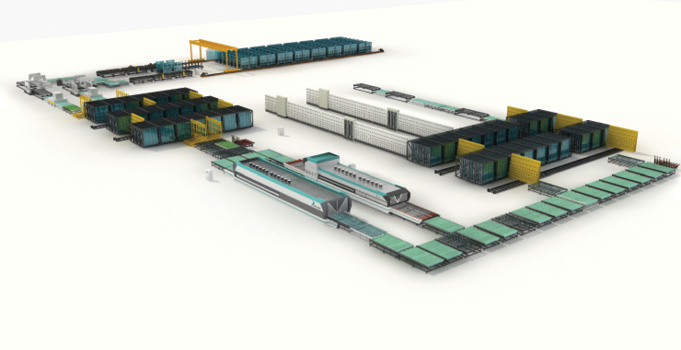
Machinery innovations
Beyond automation and flexibility, machine manufacturers have focused efforts on developing equipment to meet demand for various glass product trends. Several sources mention the rising demand for extra-jumbo capable machinery, as well as machines that can run thicker glass. Others note that customers in laminated glass are moving away from strictly using PVB to using a wider variety of interlayer materials, while other customers are using more advanced products such as electrochromic glass and are seeking technologies to produce these products at a lower cost.
Additional machine improvements look at quality and safety, says Erdman’s Donohue, but speed and production barriers are being broken as well. “We are seeing off-the-shelf 6-axis robots being used for what would have been a dedicated 3- or 4-axis application in the past,” he says, citing the competitiveness of 6-axis robots.
Vertical CNC machines are enjoying a rise in popularity, according to David Anderson and Mike Rosato, directors of machinery sales engineering at Salem Flat Glass & Mirror. One of its machines, the Denver Advance, has what they describe as “a good ratio of the space it takes on the floor to size of piece it can produce. It also allows for zero suction cup set-up time and the continuous operation of pieces such as shower doors and railings. This type of machine is evolving to meet customer demands and is becoming prevalent throughout the industry.”
The next generation of manufacturing equipment also may be on the horizon. “The most exciting trend we’ve seen is the increase in companies working to develop new technologies and branching out from the tried and true methods of production that have been around for decades,” says Burkholder. “We have been spending a lot of time talking to companies recently about providing them with equipment for R&D rather than full-scale production.”
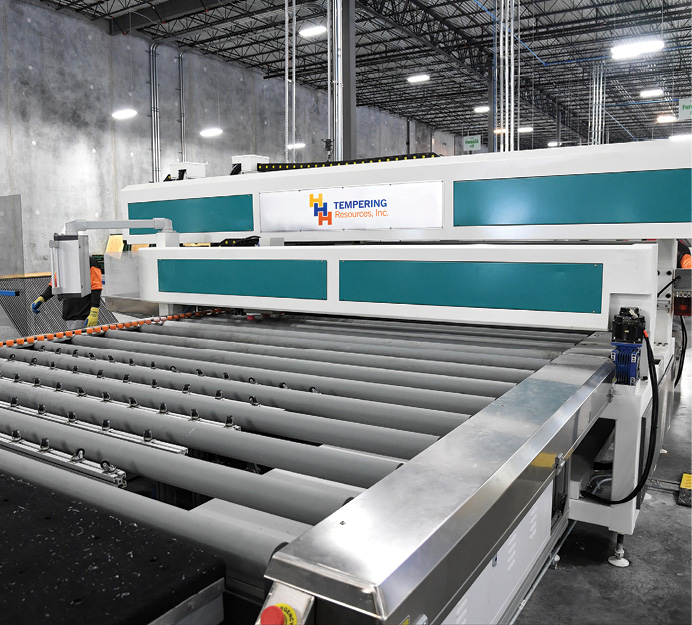
Efficiency
Time is money, and this is especially true on the manufacturing floor. Efficiency gains often translate directly into increased revenue. “At the end of the day, it’s about making money, and you need to be efficient to make money,” says A+W’s Rudd. “With the labor pool the way it is, you better make your employees as effective and efficient as possible, and that’s what technology and equipment does.”
“Overall, there is a real move toward efficiency,” say Anderson and Rosato. “Efficiency of order entry, efficiency of part programming, efficiency of CNC tool application and sequencing. There is a strong movement in the direction of reducing inputs and processing steps, handling, and the ability to produce precise and repeatable efficient processes.”
Not only does automation enhance efficiency internally, but it also provides transparency for customers and a 360-degree overview of production, says Guschlbauer, so that customers also can track the entire status of their orders online.
Moreover, continue Anderson and Rosato, robotics and automation “tend to grow production output exponentially as well as decrease rejects, reworks and lates, which, in turn, increase customer satisfaction and profitability.”
Rudd also sees lean manufacturing as an important element of efficiency and having the proper equipment and software in place to be able to reduce breakage or errors in the shop, and be able to bounce back quickly in the event of one. “When you tie design directly into a machine where you can steer machines, not re-keying, you eliminate mistakes,” he says. “A big part of lean manufacturing is reducing footsteps and eliminating mistakes.”
Fabricators demand efficiency improvements for specialty equipment as well. Fabricators often ask up front if protective glass coatings are applied using automated machinery—a drastic difference from only five years ago when many coatings were still hand-applied, observes Syndi Sim, vice president of marketing and business development at Diamon-Fusion International. “Fabricators are realizing that to stay competitive, they can no longer afford small inefficiencies, human error and, conversely, they need to maximize their dollars spent,” she says. “Implementing automated machinery accomplishes that.”
Market pressure and the challenge to do more with less are top-of-mind for many, as well. “Our customers realize that automating processes improves speed and quality for an on-demand world that prioritizes individuality,” says FeneTech’s Miller. “By building configurable systems that can easily adapt to thousands of product configurations and still guide orders through a streamlined production workflow, fabricators can rise to the top with best-in-class service levels.”
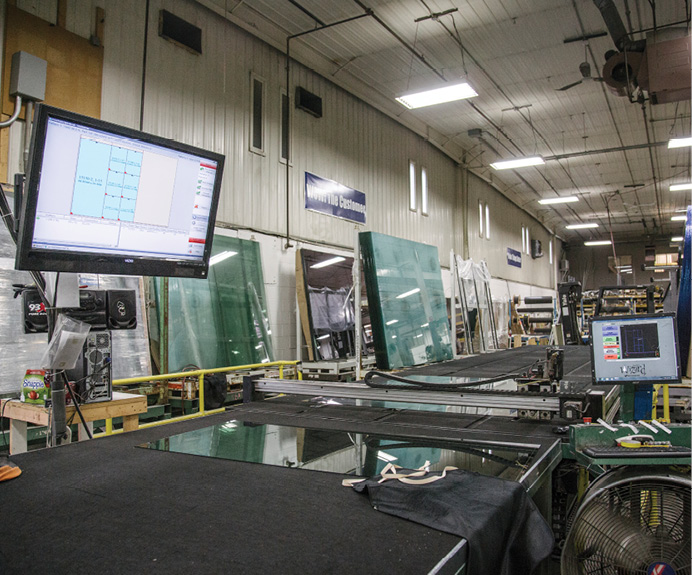
Labor pains
“The main ‘pain points’ for the glass fabricators remain the same, and include deep concerns with regards to the labor (employees) required to do the work,” says IGE’s Spellman. “It has been, and continues to be, a major challenge finding employees that are capable and responsible, as well as ensuring the safety of those employees.”
Automation gives companies much-needed flexibility to distribute limited human capital where it’s most needed. “The good thing about robotics is they punch in and never punch out. It fills up that gap when you have an employee shortage, or a manpower shortage,” says Synon.
Much of today’s modern machinery can also excel where humans don’t perform as well, such as glass quality inspection, says Huffman of Softsolution, which is currently working on a new tempering quality inspection. “The level of inspection required now can no longer be performed by a human being,” he says. “Recent developments in quality checks, such as anisotropy and edge stress, cannot be manually performed at all and now special equipment is needed.”
“What is unique about the automaton and integration movement is, it does not eliminate jobs, it actually redistributes the labor force,” say Anderson and Rosato. “When a company moves to automation, efficiency and production increases. As a result, more output is needed upstream in the cutting department, which creates a need for more employees to process the glass lites. Also, with exponentially higher production rates, more glass is being fed downstream, which creates a need for more processing to get the glass on the trucks and out the door. … Even though facilities are becoming more automated, it is not really eliminating jobs; it increases efficiency and production output, allowing a redistribution and education of the workforce.”
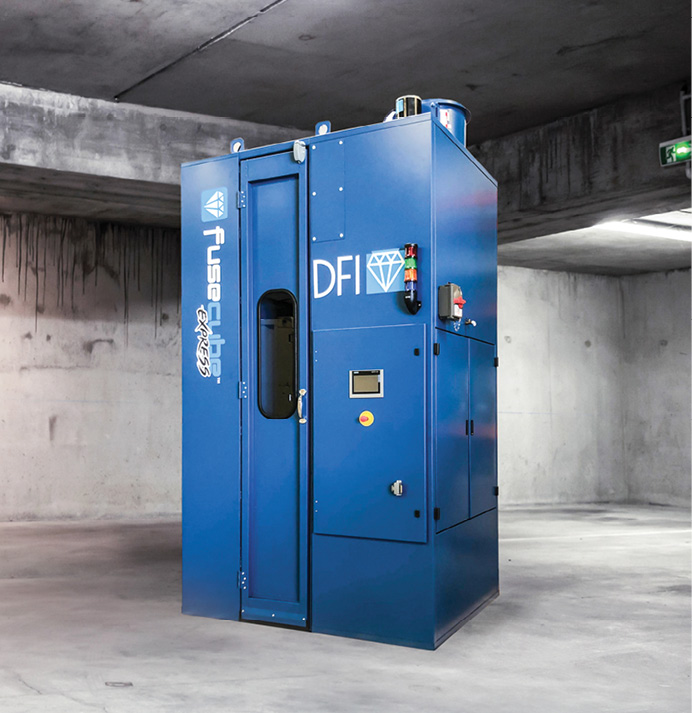
The Next Big Thing
“Large insulated glass units, lamination and, moreover, a combination [of] tempered/laminated units for safety.” —David Anderson and Mike Rosato, directors of machinery sales engineering at Salem Flat Glass & Mirror
“For sure the next big thing will be to translate the enormous amount of highly developed technologies we already see in other sectors like consumer electronics, data management, etc., in reliable solutions for the many problems glass working has; cross-contaminations will become more and more frequent and some solutions which are already latent in the mind of both manufacturers and final users because already experienced in different aspects of everyday life, will start to take form in glass machinery.” —Gino S. Gramaglia, sales manager, and Joe Gates, technical services manager, Lattuada North America
“The next big thing will be a more closed loop system that uses the information from quality inspection systems (and other equipment) to send feedback to other machinery in the process. The different production machinery will then start to use the data to self-adjust and learn to react accordingly.” —Nate Huffman, president, Softsolution North America
“There is a lot of interest in thin film coating technologies with a focus on making electrochromic glass cheaper to produce.” —Derek Burkholder, vice president of sales/engineering, Casso Solar Technologies
“In addition to increasing communication on the shop floor, our customers want to improve integration and communication beyond the walls of the building. This includes notifications to outside resources, mobile apps for tracking deliveries, and tighter integration with vendors.” —Dave Miller, group manager – business development executive, FeneTech
“We have to continue to not only produce at greater speeds but with fewer people. Those with the best units-per-person numbers will be the winners. We are working on making highly automated solutions using just one person in a small space.” —Morgan Donohue, president of Erdman Automation
“Definitely a bigger push toward robotics and full automation as much as possible. Finding people is getting harder and harder.” —Mike Synon, president and CEO, HHH Tempering
“Single-pass machines are a good bet. They allow for a high print quality combined with fast, mass production capabilities.” —Yariv Ninyo, head of business development, Dip-Tech
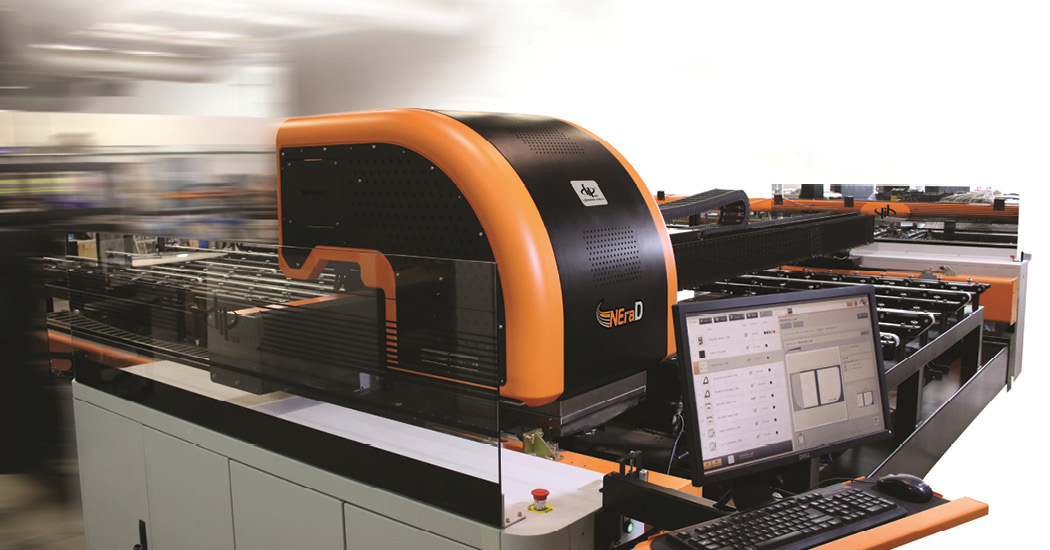
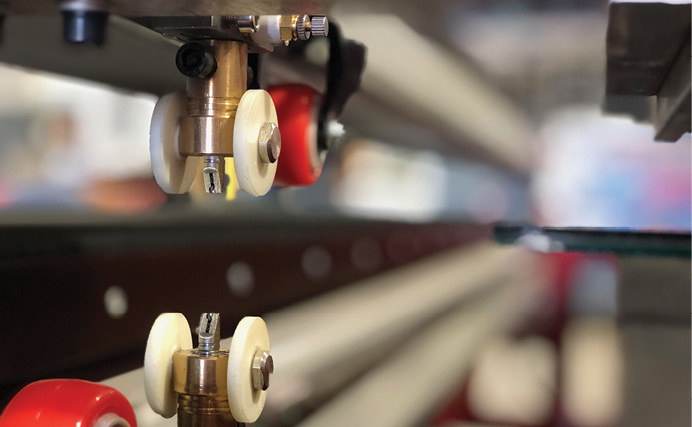
How the Coronavirus Legacy Influences Automation Today
One of COVID-19’s longer-term effects appears to be that of continued social distancing. Dave Miller, group manager – business development executive at FeneTech, says: “Now that companies are beginning to open back up, the conversation is shifting to how to maintain social distancing on the shop floor while not losing gains that have been made in efficiency. Work cell automation certainly helps in this area; however, advanced systems are required to deliver the appropriate processing information, unit by unit, to the automated work center. Additionally, the ability of these automated work centers to send data back to the production system provides opportunities for more flexibility and better management in the workflow.”
Erdman Automation also pointed to social distancing as a driver for automation, alongside quality and safety. “Our workforce is more vulnerable and less stable than in years past and, in order to insulate the factory production from that reality, automation is required,” President Morgan Donohue says.
Knowing a factory uses automation also may give the customer more confidence. “When it comes to automation, limiting touches is the name of the game,” says Syndi Sim, vice president of marketing and business development at Diamon-Fusion International. “Since COVID-19, the need for automation has become even more imperative. Promising customers a safer, hands-free assembly—from building to installment—will build confidence among your customers, whether it’s the glass shop, architect, building owner, designer or homeowner.”
The service space also benefited from technology during the pandemic. “Products like the Lisec.eye help solve machine errors quickly online and via video function,” says Claudia Guschlbauer, head of corporate marketing and communications at Lisec. “Thus, no man is needed onsite in the first step or repairs can be carried out independently.”
Automation, already in a growth mode prior to COVID-19, will see significant growth, according to Michael Spellman, president, IGE Solutions. He points both to automation’s ability to help with the labor shortage, but also for human resource-related concerns, including associated potential legal actions against employers in light of COVID regulations. “The pandemic has brought to the surface more HR pain, as well as more pressure for profitable production,” he says.
Another trend during COVID-19 that some sources expect to continue is that of the need for local service and parts. “The trend we see from fabricators is service and maintenance has become a big issue due to COVID-19. People need local service,” says Mike Synon, president and CEO of HHH Tempering.
Erdman’s Donohue agrees, citing the pandemic bringing to light North America’s “vulnerable” supply chain, not only with components, but also with machinery and supporting services. “It is easier to support machinery that is produced here in North America because all the parts are typically sourced locally,” he says. “The technicians who assemble and support the machines reside in the same relative time zones and there are no language barriers.”