Do’s and Don’ts for New Machinery in 2020
Work with vendors to seize new opportunities
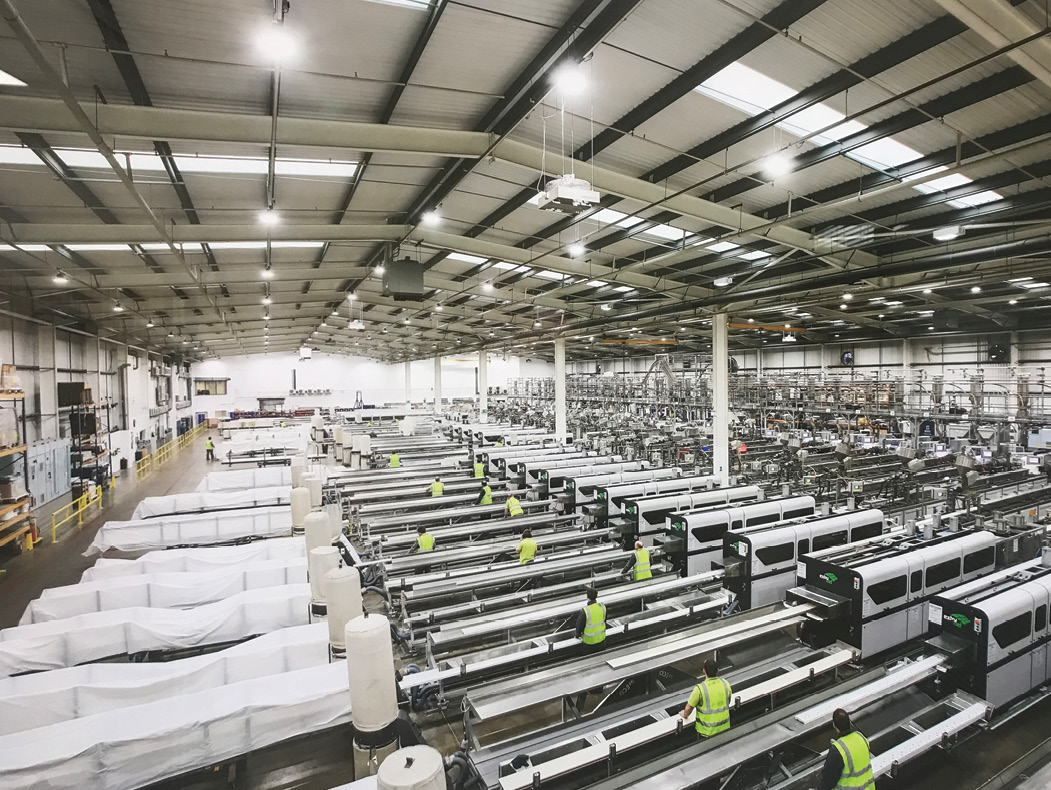
The factory of the future is a hot topic of discussion and is an aspirational goal for many industrial operators. The future factory features high-speed, efficient, automated machines whirring away, connected by the Internet of Things. Shop floor workers, rather than piecing together products with their hands and tools, are busy working with software to ensure that all processes are flowing as they should. Logistics and shipping are optimized at every level.
Many of today’s commercial glass manufacturers aren’t quite at this level of sophistication, but companies are getting closer every day. Glass shops around the world have made the investment in high-speed insulating glass lines and other forms of automated equipment. Many others are likely considering doing so very soon. Some may have made the purchase over the winter and are awaiting installation from the OEM in the coming months—just in time for busy season.
For manufacturers making investments in their factories, there are a few do’s and don’ts to think about when it comes to getting the most from today’s top commercial glass machinery.
DO: Ensure IT compatibility with existing equipment and systems.
If a company is awaiting installation of new equipment, owners and managers must make sure they are doing their homework on the IT side of the operation. The new equipment needs to be compatible with existing systems, and decision makers should ensure any necessary software updates have been completed so they are ready to start production right away.
DON’T: Neglect older equipment.
Not many commercial glass producers are completely overhauling all equipment at once. While it can be easy to become preoccupied with ensuring new equipment is up and running as intended, priority must still be placed on numerous older and still-reliable machines and equipment that help make quality commercial glass. Keep up those maintenance schedules.
DO: Optimize plant flow.
The installation of new equipment provides a great opportunity for manufacturers to rethink plant flows and processes. One consideration is a straight-line approach, such as that provided by vertical high-speed IG lines. Because supervisors can see straight down the line, they know what is happening with in-production units at all times, allowing them to easily spot any deficiencies. The straight-line approach can and should be applied across the plant, where possible, minimizing the number of touch points and the distance units need to travel from point to point across the plant.
DON’T: Assume “business as usual.”
New equipment probably means manufacturers will need to adjust some of their typical processes. Shop floor workers will need some training on how to best work with new machinery. If the manufacturer is adding capacity to a line, that means raw materials ordering and fulfillment will need to be adjusted, too. Owners and managers should work with vendors to make sure they have what they need to maximize new capabilities. Above all, keep an open mind. Advanced new equipment may open doors to new opportunities for glass manufacturers—be open to where those doors might lead once the equipment is up and running.
DO: Prepare the sales teams.
The benefits of new equipment extend beyond just the shop floor. Oftentimes, high-tech machinery can help a company make a higher-performing product—which means the sales teams must have the knowledge to convey those benefits to customers. The sales teams must be armed with the right information and knowledge to clearly communicate the benefit of the improved product to discerning customers.
New machinery brings new opportunities. Manufacturers should work with vendors to make sure they are fully capable of seizing them.