Flat Glass Recycling
It’s possible, it’s profitable, and it’s necessary to achieve energy efficiency targets in glass manufacturing
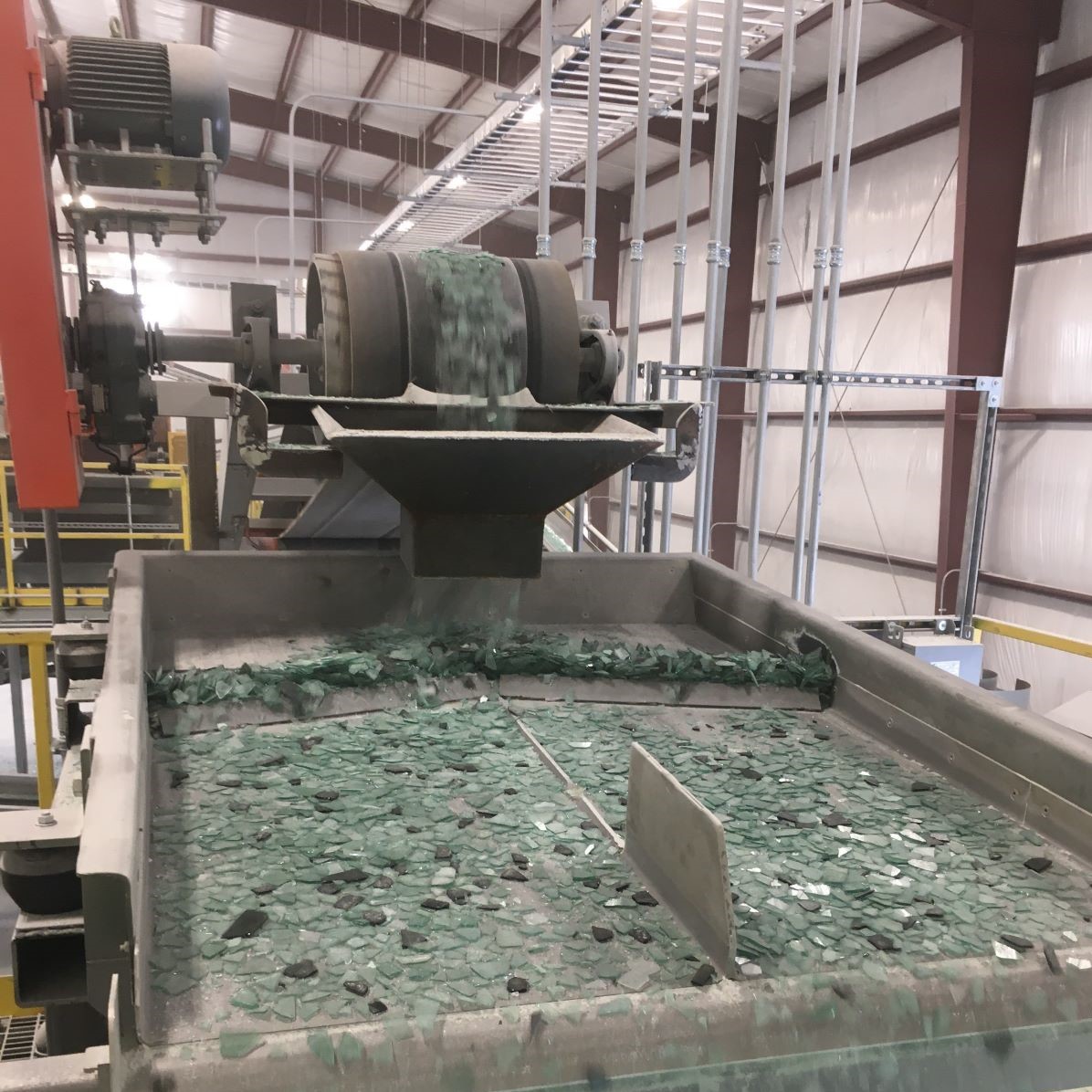
Above: Recycling operations at the Fuyao Glass America Moraine, Ohio, Facility. SMI processes the glass and returns it back to Fuyao's manufacturing process. Photos courtesy of SMI.
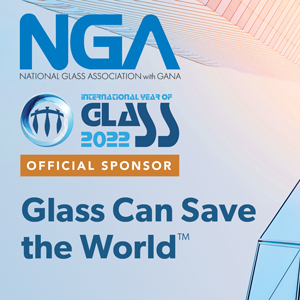
Increasing rates of recycling for flat glass offers benefits to companies, the industry and the environment. However, significant challenges remain, including education gaps about what can be recycled and how, disconnect between the glass and recycling industries, and a near complete lack of recycling of flat glass products that have reached their end of life in the field.
“The glass recycling business is good, but we are missing opportunities,” says Curt Bucey, executive vice president of Strategic Materials. “Our biggest limitation right now is getting enough feed stock. There is almost no place in the nation where we aren’t looking for more material. We need to get the message out that glass recycling is important.”
Why recycle flat glass?
Industry experts point to several key benefits of flat glass recycling, starting with limited raw materials. “With the realization that all raw materials are limited (even glass’ raw materials are limited: sand, lime or calcium carbonate, and soda ash), recycling of finished products becomes more and more important and urgent,” says Luc Moeyersons, manager for Belgium-based Lami-Solutions.
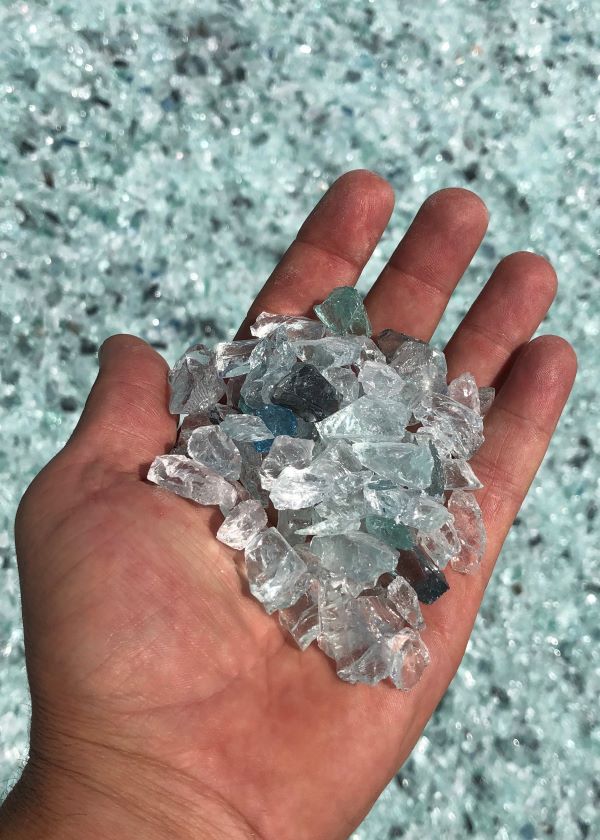
Second, “recycling flat glass saves energy in the glass melting process,” according to Bertrand Cazes, secretary general of Glass for Europe, also during a presentation at NGA Glass Conference: Long Beach.
According to Cazes, manufacturers can achieve a 2-to-3 percent reduction in energy consumption for every 10 percent of recycled glass cullet used in the batch. Looking another way, 1.1 tons of cullet can save 1.3 tons of raw materials and reduce CO2 emissions in glass manufacturing by 340 tons, he says. “This is only focusing on manufacturing. If you look upstream at the mining for raw materials that aren’t used, you’re achieving much higher CO2 savings,” he says.
Finally, recycling can provide a cost savings for glass companies. For manufacturers, savings come through reduced energy use. “Cullet is used continuously in float ovens to reduce the oven bath temperature and emitted CO2,” says Moeyersons. “Adding 40 percent cullet allows [manufacturers] to reduce the oven temperature to 1,150 degrees Celsius, down from 1,600 degrees Celsius.”
Down process companies can also see cost savings through recycling. “Whatever a company is paying to send waste glass to landfill, we will come in [at a lower cost] to take it for recycling,” says Bucey. “You’re doing the right thing and it doesn’t cost you.”
How is flat glass recycled?
“The first place we’d like to go with recycled cullet is back into flat glass,” says Bucey.
However, the flat glass sector has the highest quality requirements for cullet, presenting challenges in “how we collect, sort, and treat the glass to achieve the highest levels we can with the cullet,” says Cazes.
Within the flat glass industry, there are three origins of cullet: internal cullet (offcuts in the plant itself); pre-consumer cullet (offcuts in the downstream fabrication process); and end-of-life product (glass from an old car windshield or an old window that has been dismantled), describes Cazes. The vast majority of cullet used in flat glass is internal, coming from offcuts in the plant itself. In Europe, 75 to 80 percent of cullet is internal; 20 to 25 percent is pre-consumer; just 0 to 5 percent comes from end-of-life cullet, Cazes says.
If glass isn’t used in flat glass, it can be recycled in other industries, including container glass, fiberglass, highway beads, countertops, ceilings and walls, and more, says Bucey. “Bead is a big market for us,” he adds. “The bead industry takes it and turns it into little round spheres about the size of the head of a needle. Those are sprinkled onto the lines of the highway to make the lines more visible.”
What is status of flat glass recycling?
In the United States as of 2018, approximately 10 million tons of flat glass was manufactured, but only an estimated 25 percent was recycled as glass cullet, says Watson, and “not all of that is going back into flat glass,” he says.
In Europe, on average, float plants are running with approximately 26 percent of recycled cullet. “Five years ago, we were at 20 percent, which shows how quickly things are progressing,” Cazes says. “This is an average. There are float plants in Europe running with 40 or 50 percent of cullet in a batch. Though that also means there are others that are much lower.”
Can fabricated glass be recycled?
Almost all types of fabricated glass can be recycled, says Bucey. “In general, I don’t think we’ve ever turned down material because of coatings, because they are laminated or because they are [insulating glass],” he says. “It might affect the economics, if it has to go through additional processing. And in some cases, it limits our markets. But it doesn’t affect the recyclability.”
Watson agrees, though notes that there is a lot of confusion in the market over the recyclability of fabricated glass. “Many think that window glass is not recyclable. It certainly is recyclable. In fact, our whole business is built around recycling not just window glass, but laminated, architectural glass, IG units, etc.,” he says. “The confusion can be cleared up. But we just need some stability and viable resources.”
Moeyersons broke down the ways various types of fabricated flat glass can be recycled for re-use in float glass in a technical blog published in February. (Visit GlassMagazine.com to access the full blog.) For example, ceramic band, found in mainly automotive applications, can be present at a limited percentage in cullet and will burn off in the float oven. Insulating units must be disassembled prior to re-use. The spacers must be removed prior to recycling. However, the sealants—silicone/polyisobutylene/polysulfide—will burn off in a float oven so long as it meets certain threshold limits, Moeyersons says.
Coated glasses can be used, but some coatings may affect the final color of the glass. Meanwhile, for laminated glass, the glass cullet itself can be re-used. However, the PVB itself might prove more difficult to recycle as “after crushing laminated glass, 4 percent of the glass fragments remain on the PVB,” Moeyersons says. “Introducing glass fragments to a PVB extruder would damage the inside of the extruder and block the PVB melt filter.”
What contaminants should glass companies avoid sending out for recycling?
The first contaminant to avoid is any type of metal. “Aluminum can create infusible particles on the glass ribbon, making it unfit for sale and non-recyclable in flat glass furnaces. Stainless steel contains nickel that can create ‘spontaneous’ glass breakage in tempered glass; tungsten can lead to deposits that make the glass not sellable. And lead can lead to deposits that can attack the glass,” explains Moeyersons, in the blog.
Additionally, watch out for borosilicate glass and ceramic glasses, such as those used for fire-rated architectural applications, appliances or fireplace products. Consult with manufacturers of these specialty glass products to participate in their specific recycling programs with safeguards to segregate according to the glass type. Other “doubtful products” include digitally printed glass, smart glass and electronic mirrors, says Moeyersons.
In general, “to evaluate product quality and ensure good separation of the various contents, float glass producers use, and prefer to use, official recycle companies,” says Moeyersons.
Where does the industry go next?
For the glass industry to increase the amount of recycled cullet used in flat glass manufacturing, Cazes recommends focusing on pre-consumer and end-of-life cullet. He attributes the European glass industry’s recent increase in use of cullet to improvements in collecting pre-consumer cullet “by working with fabricators and processors to make sure all offcuts are separated in separate bins and collected regularly, directly by float glass manufacturers themselves. The truck comes, delivers the glass, goes back with cullet. That’s the easiest way,” he says.
However, the greatest potential gains can come “by focusing on end-of-life glass,” Cazes says. Less than 5 percent of end-of-life glass is recycled in Europe, he says, and only a negligible amount of that recycled cullet is used in flat glass.
The picture is similar in the U.S. market, says Bucey. “Most fabricators are recycling. The area that isn’t recycling is window replacement,” he says. “I would love to figure out how we get the message out that we can use this glass. Instead of companies paying for landfill, pay for recycling. If you have a high-rise where you’re getting ready to rip out old windows, put a roll-off box onsite. Once it’s done, we’ll pick it up.”
No matter the path, sources are confident that flat glass recycling will continue to grow. “The industry is working hard, because it is considered essential for the future of our industry,” says Cazes. “It’s our sustainability credential, and it’s an essential [part of] de-carbonizing our own manufacturing environment.”
Sources
- National Glass Association Glass Technical Papers, “Recyclability of Architectural Glass” and “The Reusability and Recyclability of Mirror Products."
- “The Need for Recycling to Enhance Our Supply Chain, The European Experience (video),” presentation by Bertrand Cazes, secretary general of Glass for Europe.
- “Recycled Glass…It’s Not Waste, It’s the Future (video),” presentation by Jeremiah Watson, CEO, Infinite Recycled Technologies.
- “Architectural Glass Laminating Guide – Part 10: Laminated Glass – Recycling,” blog by Luc Moeyersons, manager for Belgium-based Lami-Solutions. Read on LinkedIn or download (pdf).