5 Takeaways from Safti First Facilities Tour
A company decades in the making
During AIA's A'23 conference, NGA staff were welcomed for a tour of Safti First's facilities located in Merced, California. We spent the afternoon learning about the company's variety of products and testing capabilities from President and CEO Bill O'Keeffe and Vice President of Marketing Diana San Diego, as well as learning how the company has developed throughout its decades in operation.
Here are five main takeaways after spending a day getting to know the company close-up.
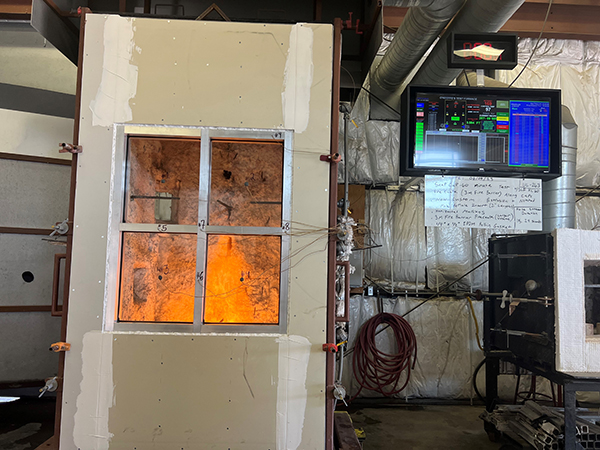
1. Safti First's president made safety a priority
Safti First's president and CEO Bill O'Keeffe has been in the business, in one way or another, since he was 14 years old working for his father's skylight business. Many years later, in 1978, he performed the first U.S. testing of fire-rated glazing products from Europe. After a series of successful tests, he formed Safti First.
During the mid- to late 1980s, O'Keeffe started to offer clear, fire-protective, CPSC Category II impact safety glazing to replace traditional wired glass in 20-45 minute applications. At this time, he also started to manufacture the clear, fire-resistive glazing locally here in the US (SuperLite II-XL), making him the first to do so.
O'Keeffe has been an advocate for public safety from the start, he says. After learning about the thousands of injuries caused by traditional wired glass, he pushed for a successful code change that now prohibits the use of traditional wired glass in doors, sidelites and other hazardous locations. He also developed clear, safe and economical tempered glass alternatives to traditional wired glass.
Read more about wired glass and safety applications.
2. Testing for fire resistance in-house
Safti First tests its glass for fire resistance in-house, in addition to third-party testing. In-house testing is done by heating the interior of the glass for one hour up to about 1,800 degrees Fahrenheit. Fire-resistant glass is supposed to react to this level of heat similar to walls. The interior of the glass may break, but the exterior will stay in tact and cool.
After the hour is up, a hose stream test is conducted. These tests are only required in the U.S. and Canada. The hose test we witnessed on the tour was done from 30 feet away at 20 pounds per square inch, but the distance and pressure depends on the specimen being tested.
While the glass window was able to stay intact and not break from this pressure, the sheetrock surrounding it crumbled, demonstrating the integrity and importance of fire-rated glass.
.@saftifirstglass tests it’s #fireresistant glass in-house. This glass was hose stream tested at 20 psi from 30 feet away. As you can see, the #glass held up better than the sheet rock. pic.twitter.com/59kCCp9uwj
— Glass Magazine (@GlassMag) June 6, 2023
3. The company is vertically integrated
Safti First, through its parent company O'Keeffe's Ladders and subsidiary Titan Metal Products, manufactures a variety of products, from fire-rated glass, to aluminum doors and frames, to ladders. These products are manufactured and tested on site.
4. New capital investments, and more ahead
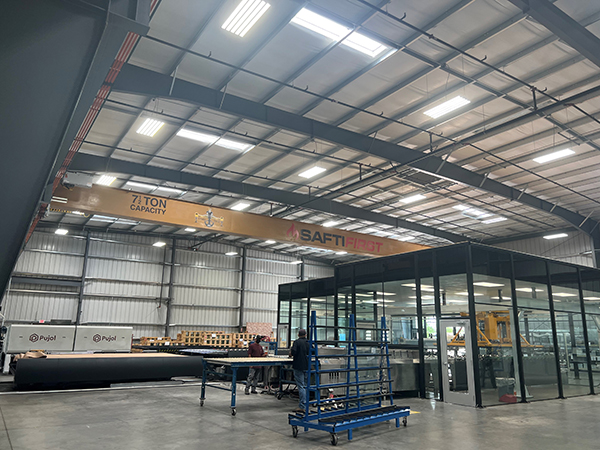
Safti First finished installing the Pujol 100+ fully automated laminating line earlier this year. It has an oven for standard lamination processes and one oven for security products.
This automated laminating line is capable of manufacturing almost any variation of laminated glass products such as bullet-resistant, blast, hurricane, forced entry/attack, glass floors, LED glass, bird-friendly glass and many more.
The company has plans to bring in a large-scale furnace within the next year. This will be placed in the research and development department by pushing one of the walls back and lifting up the roof. This furnace will allow Safti First to experiment with even larger sizes, different make-ups and additional performance tests.
5. Automation, automation, automation
Titan Metal Products, a subsidiary of Safti First, has made a recent switch from manual to automated when it comes to manufacturing its fire-rated doors. The company also uses a laser punch machine that operates on its own with little supervision or intervention. This allows for cleaner, sharper edges, say company officials.
Safti First also has a water jet that can cut up to nine-inches of steel. The company's newest laminating line is also automated.