How to keep people cool with thermally broken framing
Occupant comfort translates to greater productivity
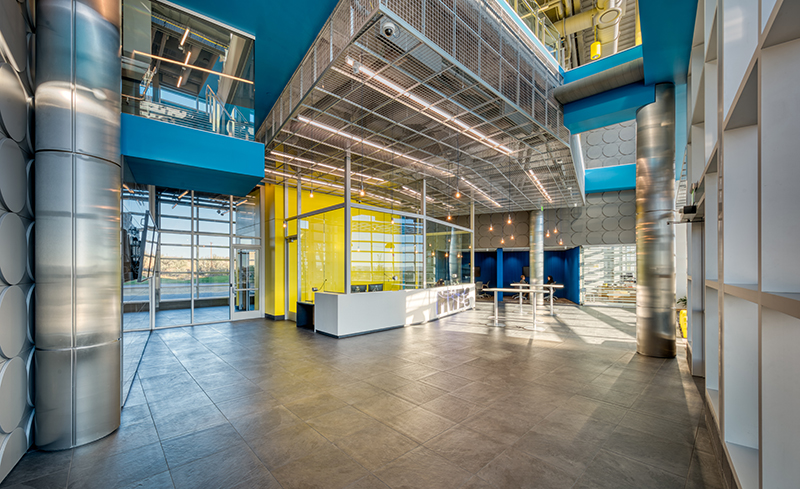
In warm climates and summer months, air conditioning and natural ventilation bring relief from the heat outside. No one wants to roast in a glass-enclosed stairwell or sweat next to a closed window.
Fenestration systems with high thermal performance create expansive openings that keep us cool and comfortable inside the building, provide outdoor views, and improve the building envelope’s energy efficiency. These attributes also align with the U.S. Green Building Council’s LEED Rating System’s criteria.
Occupant comfort translates to employee productivity
Aluminum is strong, light weight, versatile, corrosion-resistant and infinitely recyclable, but also an excellent conductor of thermal energy. To reduce heat transfer, an aluminum-framed fenestration system’s interior and exterior surfaces are separated with an insulating barrier. This is called “thermally breaking” the frame.
Non-thermally broken aluminum framing will transfer energy, causing uncomfortable interior temperatures. Uncontrolled, this can interfere with the building’s HVAC, increase energy use and costs, and lead to unproductive, irritable occupants.
People account for 90% of business operating costs, according to the World Green Building Council. This means even a 1% improvement in employee productivity can have a major impact on an organization’s bottom line. Because daylight, views and thermal comfort contribute to employee’s productivity and well-being, thermally broken fenestration can offer a high return on investment.
Typical thermal barriers
Helping achieve optimal value, the two most common types of thermal breaks are:
- Insulating polyamide strip profiles – Used as thermal barriers, these strips (a.k.a. struts) are inserted between the two surfaces of the aluminum extrusion. They are reinforced with glass fibers in three axes, supporting the framing’s structural and long-term durability.
- Poured-and-debridged thermal barriers – This method involves pouring a chemically cured resin into a cavity in the aluminum extrusion. After it hardens, the aluminum cavity is removed to create the thermal break. The cavity also may be lanced for an additional bond between the metal and thermal break.
Double poured-and-debridged barriers have emerged in response to more stringent model energy code requirements. This barrier system utilizes two poured-and-debridged cavities, further reducing the energy transfer.
For curved extrusions, installing the thermal barrier in the metal after it has been stretch-formed helps minimize stress on the thermal barrier and ensures performance as specified. Supporting quality specifications and performance, the Fenestration and Glazing Industry Alliance (FGIA) offers AAMA QAG-2, “Voluntary Quality Assurance Processing Guide for Polyamide Thermal Barriers” and QAG-1, “Quality Assurance Processing Guide for Poured and Debridged Polyurethane Thermal Barriers.”
Performance and aesthetic advantages
When thermally broken aluminum framing is matched with high-performance glass, the fenestration system’s performance is further improved in all categories, including lower U-Factors and higher Condensation Resistance Factors.
Along with the improved performance, aluminum frames utilizing polyamide thermal strip also allows some manufacturers to offer dual finishes, where different colors and techniques may be specified for each side of the aluminum’s visible surface.
Innovative manufacturers continue to develop new products and technologies to enhance both the appearance and the performance of their products, meeting the needs for best-in-class building envelope performance in any season and Climate Zone.